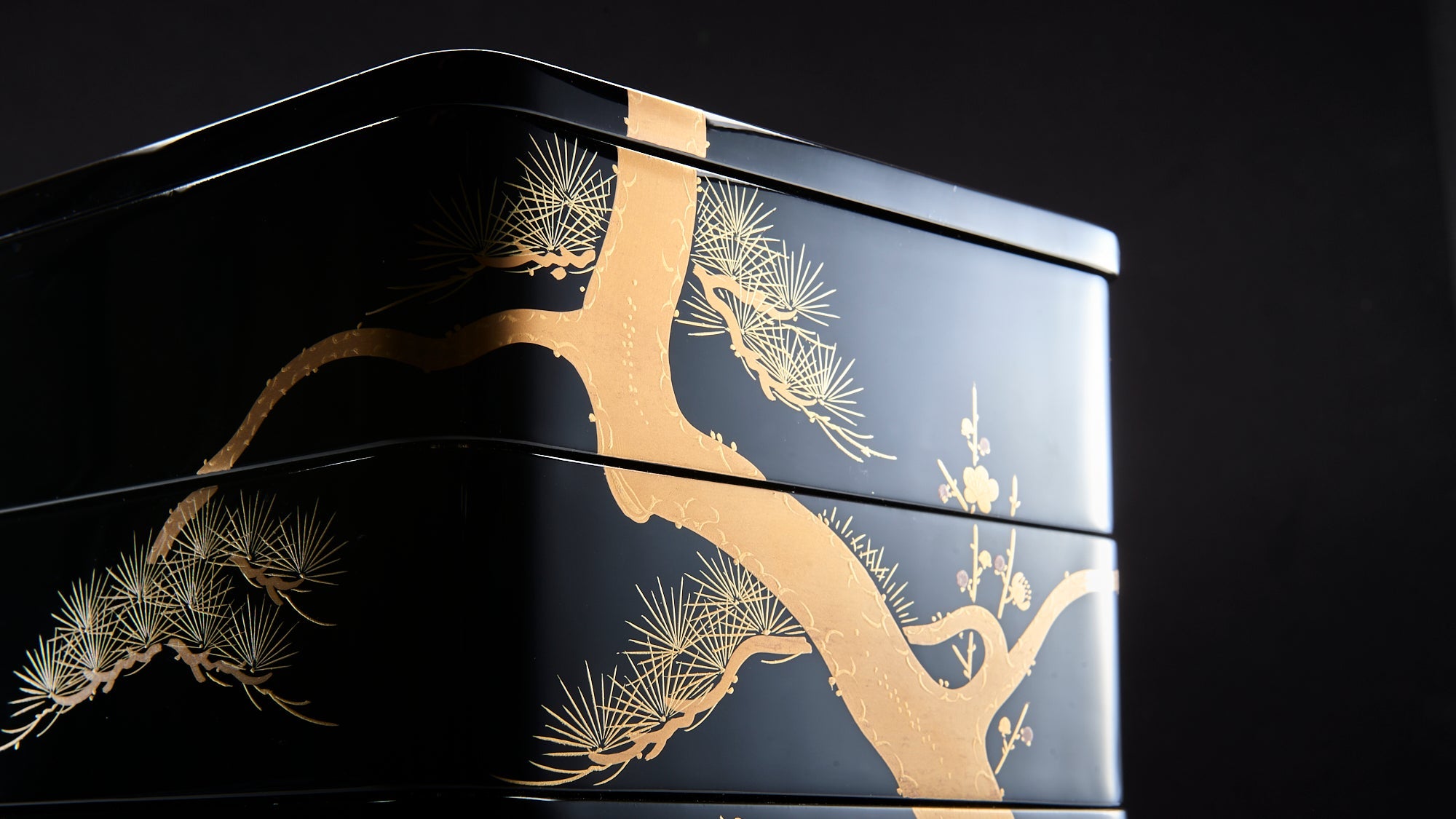
Over 1500 years of tradition as the lacquer village
Echizen Lacquerware
Echizen lacquerware originated around the city of Sabae in Fukui Prefecture, in the northern part of Japan. With a history going back more than 1,500 years, it is known for its subdued luster and elegant beauty. It is produced by experienced artisans, each specializing in one step of the production process.
Along with the changing lifestyles of Japanese people and market needs, creators of Echizen lacquerware have developed diversified products and created technology for mass production. Today, more than 80% of the lacquerware for domestic food industry and business use comes from Echizen. This is a region that is not only home to centuries of tradition, but also reinventing itself through innovation.
Echizen lacquerware was designated as a traditional Japanese craft more than 40 years ago in 1975. In Fukui Prefecture, the birthplace of Echizen lacquerware, the spirit of craftsmanship is still alive in traditional crafts such as Echizen hammered blades, Echizen chests, Echizen pottery, Echizen Japanese paper, and Wakasa lacquered chopsticks, as well as in the eyeglasses and textile industries.
Echizen lacquerware is one of these crafts that can be called the "art of the master". It requires a high level of skill and includes woodworking, lacquering, and decorative craftsmen who apply patterns and gold and silver. The strength of the lacquer, which is carefully applied over and over again, is high and extremely long-lasting. In addition, the patterns and designs drawn by the ancient decorative techniques of maki-e and chinkin (a technique in which a pattern is carved into the lacquer surface with a knife and gold leaf or gold powder is pressed into these marks) are also highly accomplished as works of art.
On the other hand, Echizen lacquerware accounts for more than 80% of the domestic market share of lacquerware for commercial use, making it the largest producer of lacquerware in Japan when commercial use is included. Echizen lacquerware can be mass-produced using not only traditional wooden lacquerware but also synthetic resins and chemical paints. The great strength of Echizen lacquerware is that it is strong enough to withstand commercial use, has a design that adds color to the dining table, and is more affordable than lacquerware from other regions.
There are many types of Echizen lacquerware. Some are luxurious and gorgeous, while others are down-to-earth and simple. Evolving with the times, this attractive lacquerware covers a wide range of needs from individual connoisseurs to restaurants.
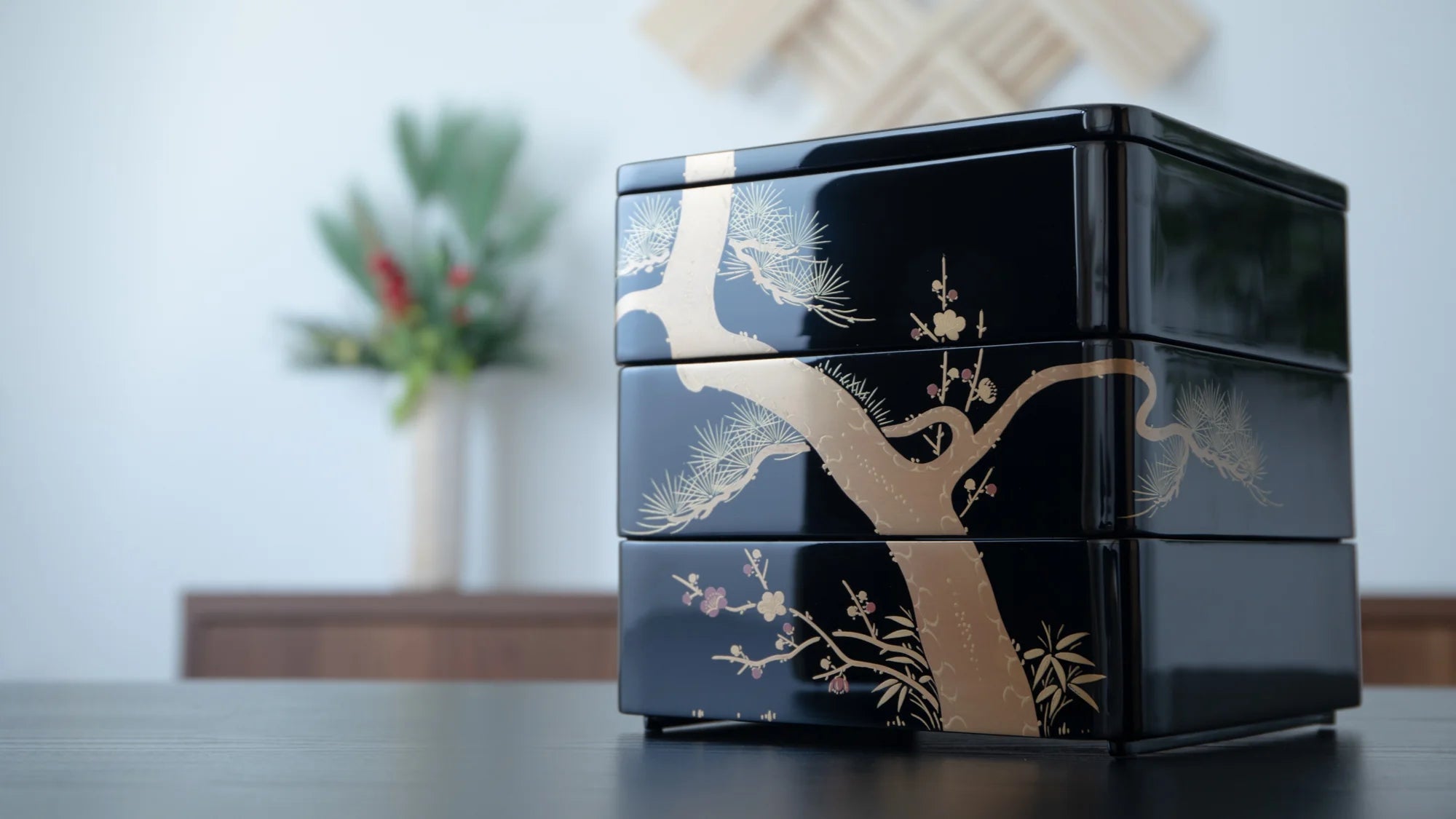
Echizen lacquerware originated more than 1,500 years ago in the Fukui village of Katayama, which is where the city of Sabae stands today. It’s said that the history of the craft started when the 26th Emperor of Japan, was still the Imperial Prince ordered a lacquerer to fix his crown. Impressed with the crown’s restoration and the black lacquer bowl that the artist sent along as a gift, the prince became a patron of the village of Katayama as a lacquerware-producing area.
Originally, Echizen, surrounded by mountains, was not suitable for agriculture, and there were many lacquer scrapers (craftsmen who collect sap from lacquer trees). Good quality wood was available, and the temperature and humidity were also suitable for making lacquerware. At its peak, half of all lacquer scrapers in Japan were in Echizen.
Records from the time of Nikko Toshogu's construction (circa 1617) include the names of people who worked as lacquer scrapers in Echizen. Because the Tokugawa Shogunate highly valued lacquer and because Buddhist memorial services were popular, Echizen became one of the leading lacquerware production centers in Japan. Gradually, the techniques of maki-e and chinkin were inherited, and robust and ornate decorations were applied.
In the Taisho era (1912-1926), with the addition of new machinery and technology, a mass production system for commercial lacquerware was established, and demand for Echizen lacquerware from the food service industry grew. Today, Echizen lacquerware has grown to account for more than 80% of the domestic share of the restaurant industry and commercial lacquerware market.

Each process of Echizen lacquerware is detailed, and the "Nushiya" is a labor-dividing organization that brings together artisans from production areas to make an item of lacquerware.
Wood base production
The first process is to select the wood. For round objects, Japanese ash or zelkova is cut on a wheel. For square objects, "Katsura", "Hoo", etc., are cut, shaved, and assembled to form the shape. It is important to properly dry the logs that will be used as materials. A craftsman, called a woodworker, is also needed, and he must have the skill to finish the work to the correct dimensions.
First coating
It is important to give the wood the first coat of paint before sending it to the painting process. The first coat of paint creates the base of the lacquerware, so scratches, holes, and natural cracks in the wood base are filled in and fragile areas are reinforced. The condition and robustness of the lacquerware coating depends on the quality of this primer.
Undercoating
The painting process is divided into undercoat and overcoat. Painting methods include hand-application and spray application. The urushiol contained in the lacquer causes a chemical reaction that hardens the lacquer, requiring high humidity. It is a delicate process that demands many years of experience because it is affected by weather conditions. Since undercoating affects the quality of the lacquerware as a lacquered object, coating and polishing are repeated many times.
Overcoating
In overcoating, it is important to quickly apply the lacquer in a uniform thickness.In order to create a glossy luster, overcoating is an important technique that dries the lacquer while maintaining the temperature and humidity. Spray coating is done with a manual spray or an automatic spray gun.
The finished coated lacquerware is dried over a period of a few days in a machine called a rotation bath which rotates at fixed times. This ensures that dirt and dust do not attach to the lacquerware.
Maki-e
Echizen lacquerware has a variety of decorative techniques, but the most commonly used are machine printing and transfer techniques such as "Maki-e" and "Chinkin". Maki-e refers to the process of soaking a brush in lacquer, drawing pictures or patterns with the brush, and then coloring by sprinkling gold or silver dust before repeatedly polishing and refining.
Chinkin
Chinkin or gold inlaying is a process where patterns are etched into surfaces using a special blade. Gold or silver leaf as well as pigments, are inlaid in the grooves, creating a fine and delicate design.

Makers
Related posts
Filters