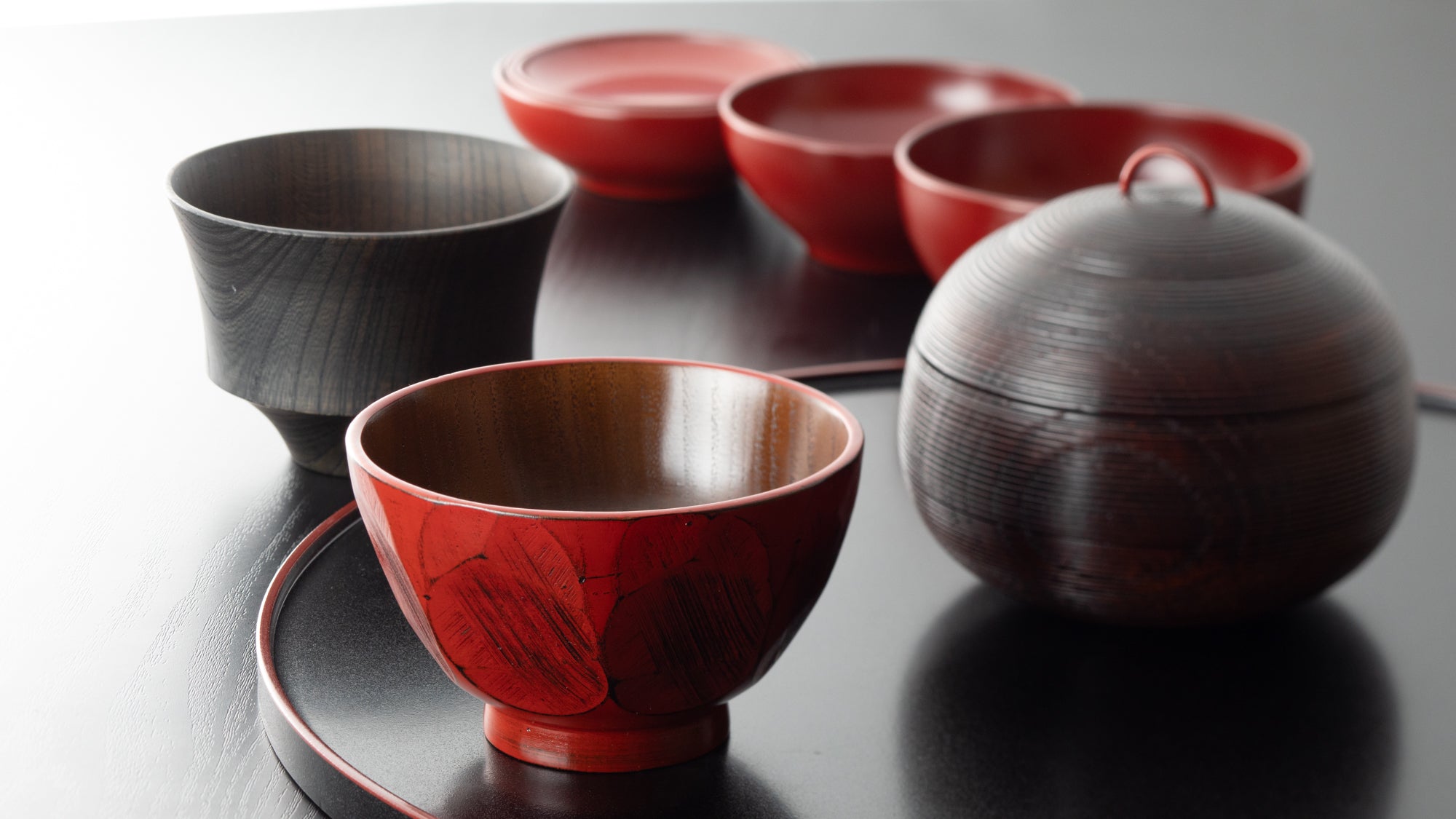
Japanese Wooden Lacquerware
Yamanaka Lacquerware
Yamanaka lacquerware, produced in the Yamanaka Onsen district of Kaga, Ishikawa Prefecture, has a proud history of more than 450 years. It is characterized by the harmony of natural wood grain and the refined maki-e technique, where gold, silver, or colored powders are delicately sprinkled to create elegant patterns.
Yamanaka lacquerware is crafted into a wide variety of items including chopsticks, bowls, plates, trays, spoons, ladles, and natsume tea caddies. It is known for being lightweight, durable, and beautifully refined. Traditional black and vermilion lacquer finishes are often used.
Yamanaka lacquerware continues to evolve, blending timeless tradition with modern aesthetics to suit contemporary lifestyles.
Yamanaka Lacquerware is made in Ishikawa Prefecture, one of the leading production areas of Japanese Lacquerware. It is called Yamanaka because it is made in the Yamanaka Onsen (hot spring) area of Kaga City. In Ishikawa Prefecture, there are two other Japanese Lacquerware production areas, Wajima and Kanazawa. Among them, Yamanaka is known as the "Yamanaka of wood”, and is the best place in Japan in terms of woodworking techniques.
The characteristic of Yamanaka Lacquerware is the wood grain processing. By hollowing out the wood in such a way that the grain runs vertically, Yamanaka lacquerware produces robust, thin, and delicately formed vessels that are not easily distorted by drying.
Yamanaka Lacquerware is also known as "Yamanaka-Nuri" in olden times, was born about 400 years ago in the Azuchi-Momoyama period (1568-1600).
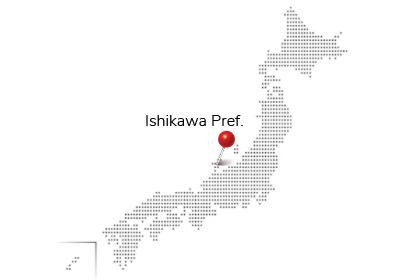
It is said to have originated when a group of wandering craftsmen called “Kiji-Shi," who made a living by making wooden vessels using a wooden wheel, settled in a place called Masago, upstream from Yamanaka Onsen. In the Edo period (1603-1868), lacquering and maki-e techniques were introduced from Aizu, Kyoto, and Kanazawa and developed into Yamanaka Lacquerware, and various techniques were invented. Then, around the Meiji period (1868-1912), the current style of Yamanaka Lacquerware was formed.
In 1913, due to the opening of the railroad, it became easier to source raw materials for lacquerware, and the production of inexpensive mass products began. However, by the Taisho Period (1912-1926), Yamanaka Lacquerware had become the official Lacquerware of the Japanese Imperial Court. In 1981, Yamanaka Lacquerware became the largest producer of lacquerware in Japan.
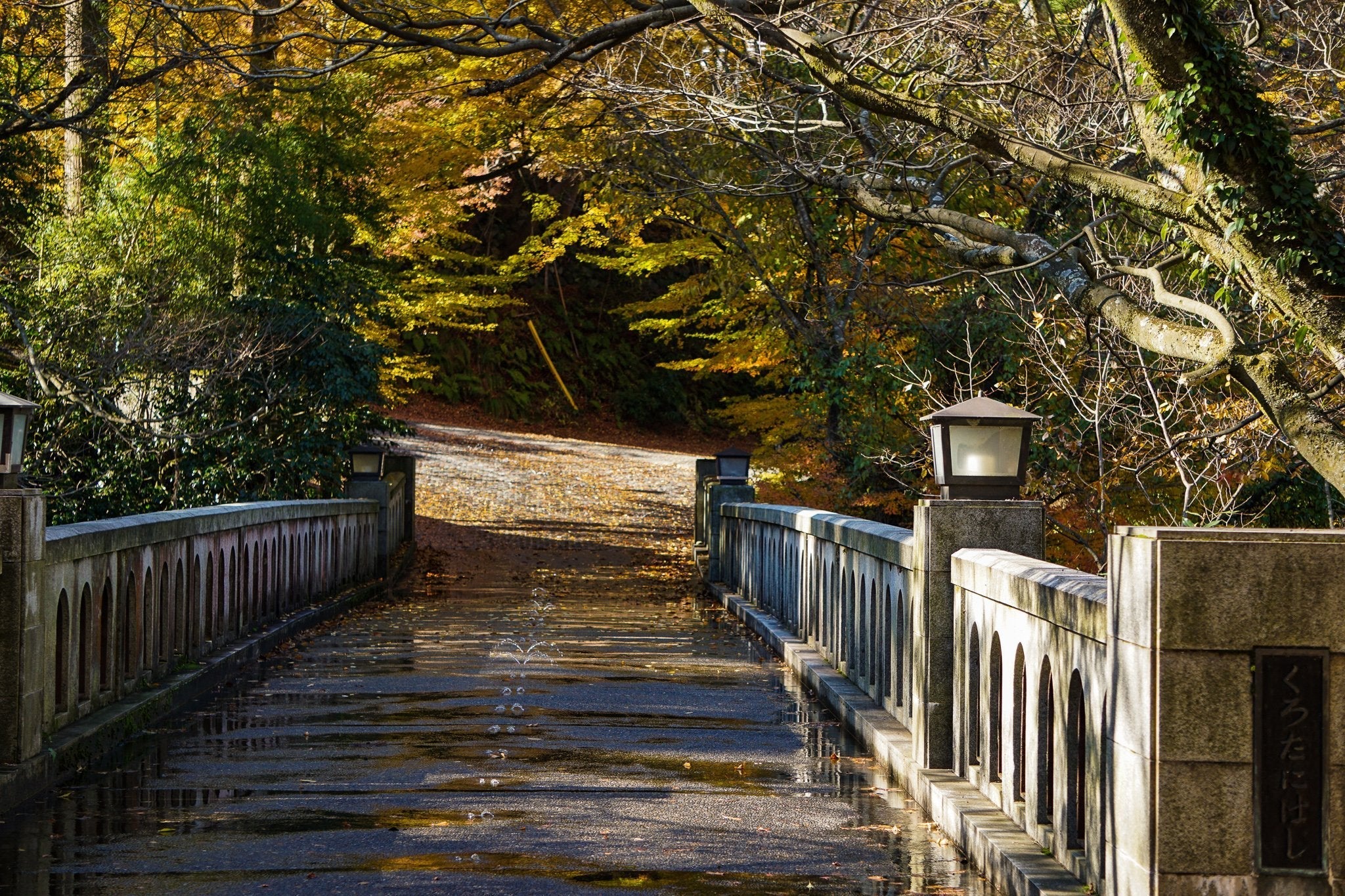
Yamanaka's Wooden Lacquerware Craft
Yamanaka's woodworking techniques are said to be the best in Japan. Have you ever seen such thin woodcraft that you can see through the light? The delicate wooden vessels are made possible by the high level of skill and dedication to sharpness of the craftsmen, who start from forging their own tools from steel.
Since its founding, Yamanaka Lacquerware's woodworking has been characterized by the technique of grinding wood on a lathe. Based on a technique called "Kiji-Biki", which involves carving fine concentric lines when carving on a lathe, Yamanaka Lacquerware has various types of carved designs, including the "Sensuji", which is a typical Yamanaka lacquerware design with a striped pattern carved vertically.
Working Processes of Yamanaka Lacquerware
Also, Yamanaka Lacquerware is made by a division of labor among craftsmen, starting with the Kiji-Shi (woodworkers). In addition, there are Shitaji-Shi (base craftsmen) who make the base of the lacquerware, Nuri-Shi (lacquerers) who apply the lacquer and finish the lacquer, and Makie-Shi (maki-e lacquerers) who do the maki-e. Yamanaka lacquerware, characterized by the natural beauty of the wood grain and elegant maki-e, is made by these craftsmen.
"Kiji-Shi" Woodcarver
Woodcarvers are known as "Kiji-Shi” in Japanese. Using good quality domestic zelkova, horse chestnut, cherry, chestnut, etc., the wood is cut to fit the shape of the vessel to be made, dried, and then hollowed out while turning on a lathe using a plane or knife.
The traditional Yamanaka lacquerware technique called "Kasyoku-Biki," in which the surface of the wood is decorated with the spinning of the lathe, gives beauty and prevents slippage, and is one of the characteristics of Yamanaka lacquerware.
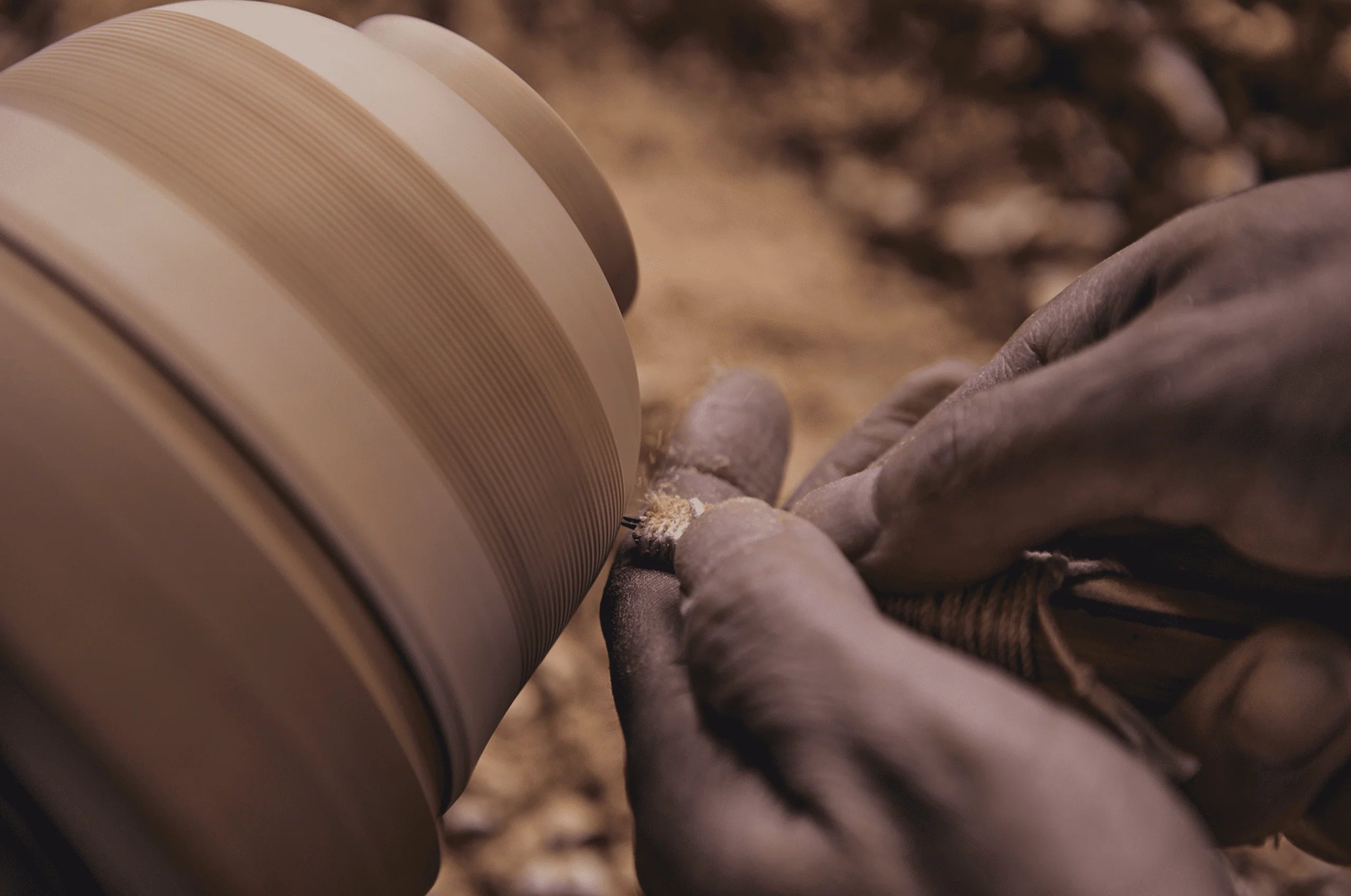
"Nuri-Shi" lacquerer
Once the base is prepared, it is time for the lacquerer, ”Nuri-Shi", to apply the Japanese lacquer. This is the process of applying the Japanese lacquer with a brush, and it is a process that requires control of the humidity to allow the lacquer to harden and full concentration of the mind to prevent dust and dirt from sticking to the surface.
One of the technique called "Fuki-urushi" is a way of applying lacquer that makes the best use of the beauty of the wood grain, in which the process of applying and wiping off transparent lacquer is repeated many times to allow the lacquer to soak into the wood grain.
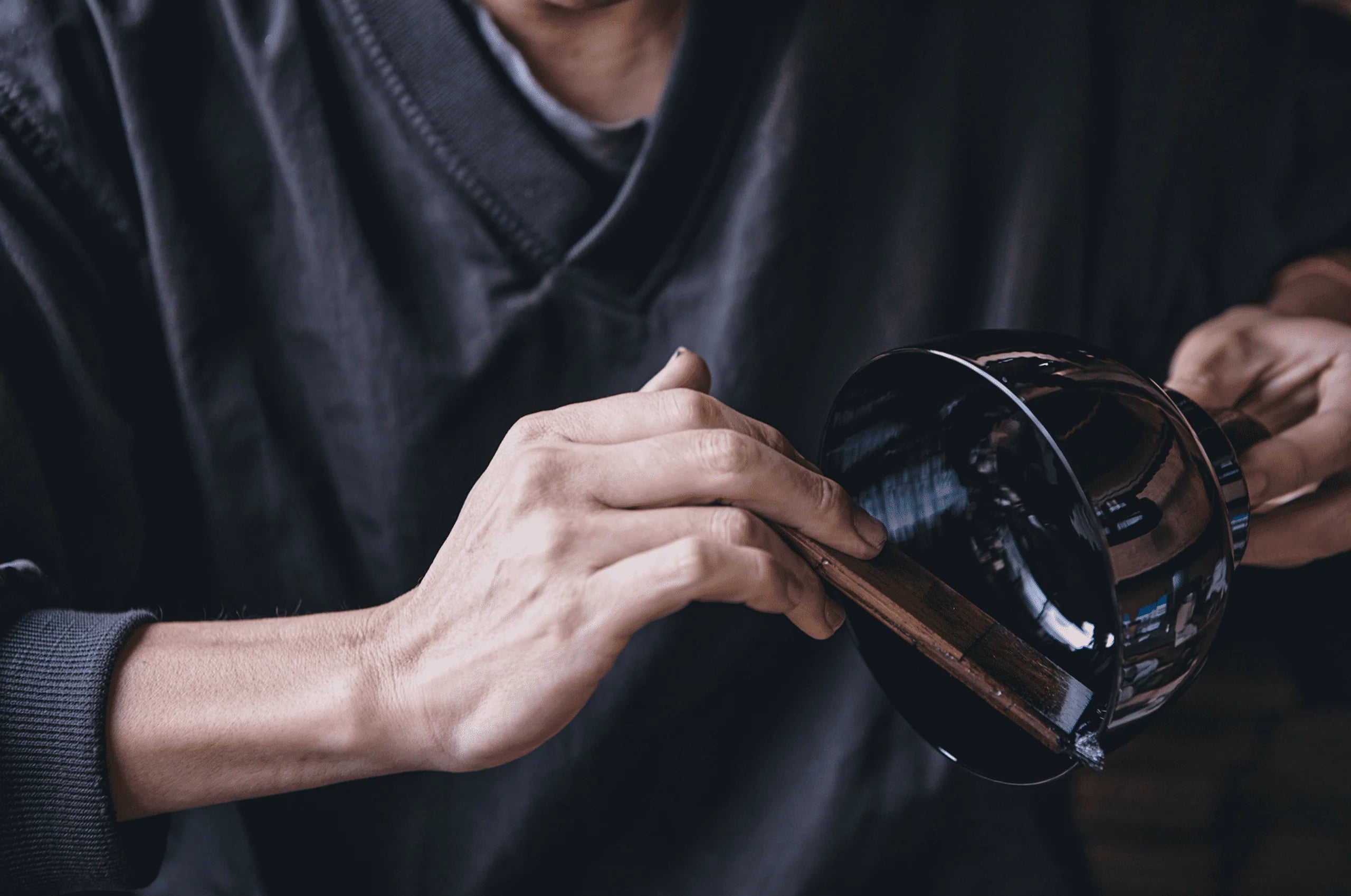
Maki-e Artist
Beautiful maki-e is the work of a specialized craftsman, "Maki-e Shi". First, a rough sketch is copied onto the surface of the finished Japanese Lacquerware and patterns and letters are drawn using Japanese lacquer. Then, while the lacquer is still hardening, metal and colored powders such as gold and silver are sprinkled on the surface. After that, it is coated with clear Japanese lacquer and polished carefully.
There are a variety of Maki-e techniques in Japan, and Yamanaka Lacquerware is famous for its "Taka Maki-e" technique, which gives a three-dimensional effect.
Photos by Yamanaka Japan
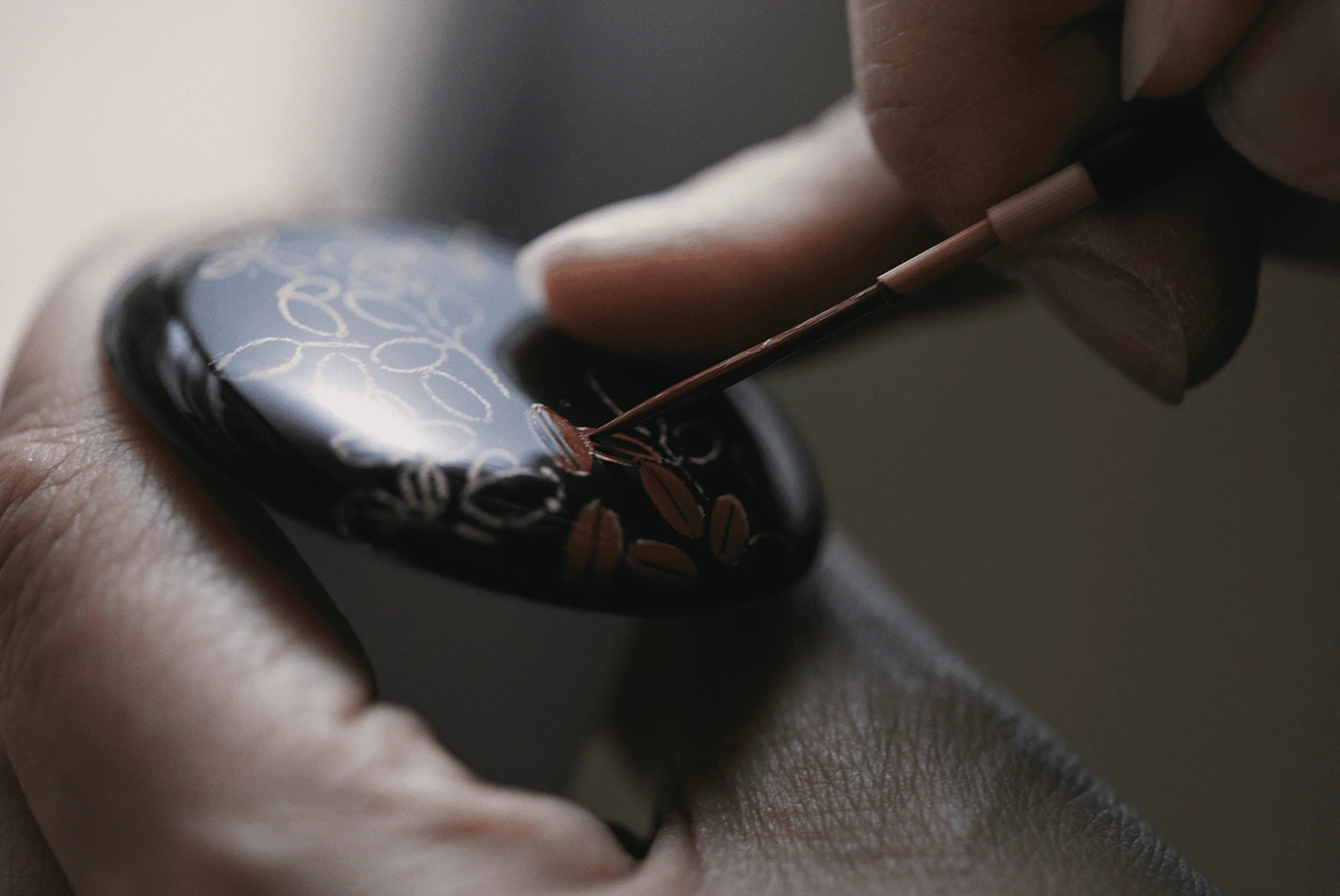
Related posts
Filters