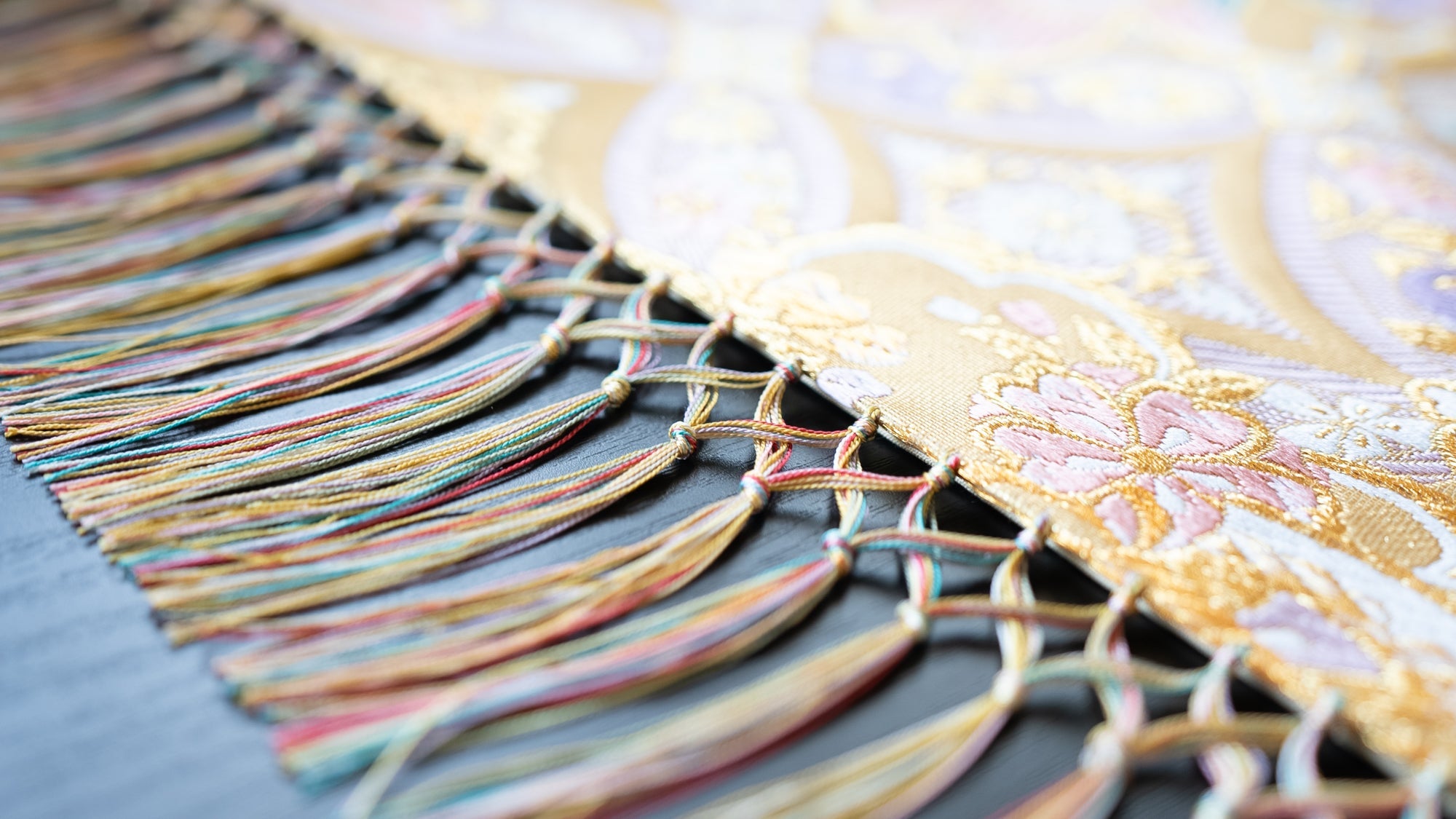
Luxury Silk Textile of Traditional Culture of Kyoto
Nishijin Ori Brocade
Nishijin Ori is a yarn-dyed brocade produced in Nishijin, the northwest area of Kyoto. It has a long history, dating back to the Heian period (794 CE –1185 CE), and is characterized by the use of beautifully dyed threads and patterns woven using a variety of techniques.
Because it is produced in small quantities in a wide variety, Nishijin Ori is highly scarce and valuable. This fabric can be cherished for an extended period of time, often being passed down from one generation to the next.
In 1976, it was designated as a Japanese traditional craft, and today, this luxurious three-dimensional woven art is widely known around the world as a representative silk textile of Japan.
The charm of Nishijin Ori is the beautiful three-dimensional patterns which are precisely planned by the yarn-dyeing technique (weaving the pattern after dyeing the threads). It is more durable and wrinkle-resistant than pieces dyed after they have been woven which is the more common method of production. And it is this detailed and meticulous craftsmanship that makes Nishijin Ori a very luxurious and artistic textile.
Instead of mass production, Nishijin Ori is crafted in small quantities, utilizing a division of labor. The products are known as the most authentic and beautiful textiles for Obi belts for kimonos in Japan because of its beauty of color using more than 50 colors of threads and patterns precisely woven.
Moreover, in its history of more than 1,000 years, Nishijin Ori has produced a diverse range of decorative textiles, and has made great strides in tradition, such as the introduction of jacquard weaving in the Meiji era (1868-1912). Today, in addition to Obi belts and other traditional Japanese kimono items, Nishijin Ori is also utilized in modern clothing, table accessories and decorative items such as lucky cats and Daruma dolls.
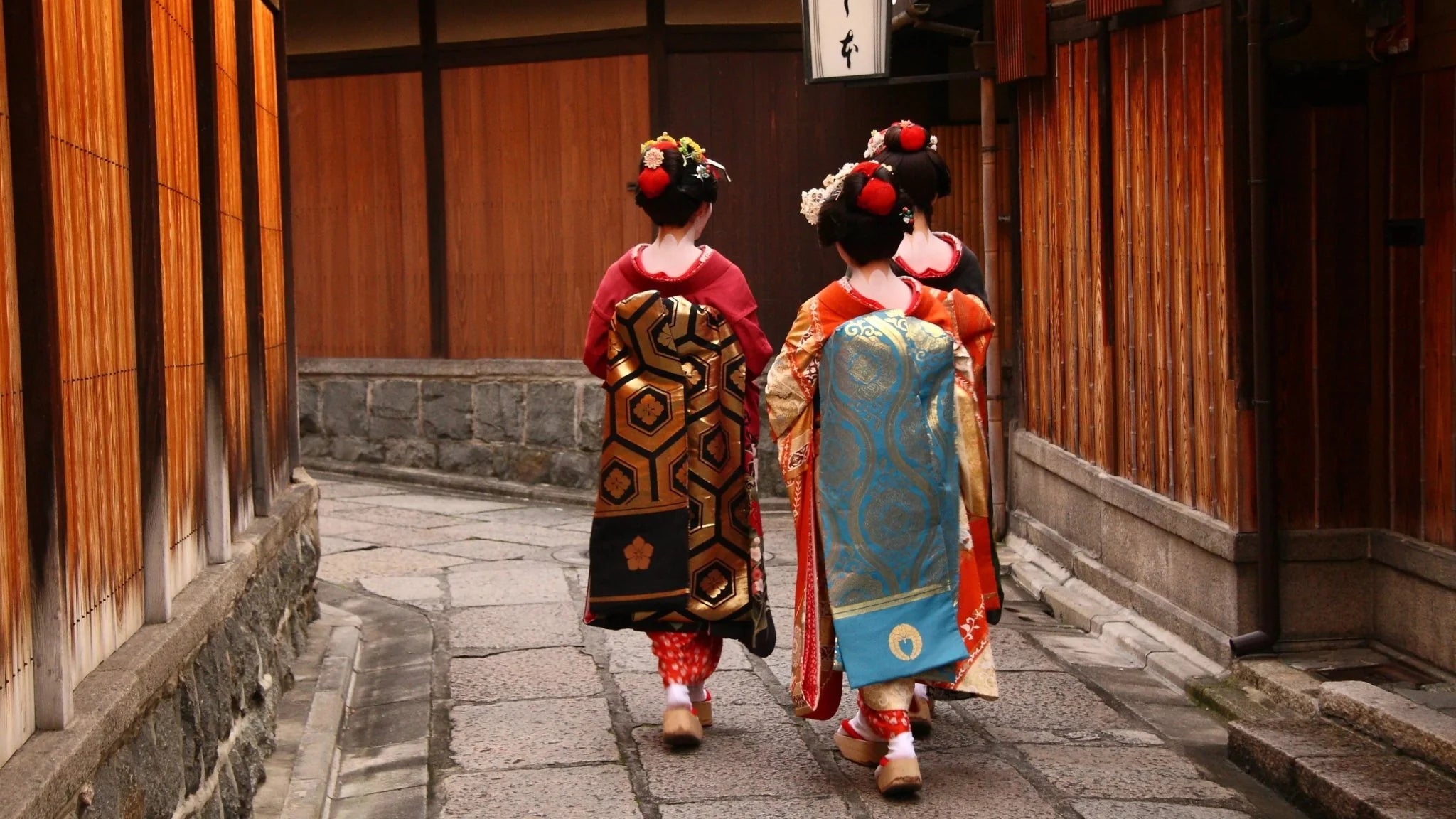
Traditional Practices of Nishijin Ori
There are a number of work processes and their terminology involved in the production of traditional Nishijin Ori, so let's go through them step by step.
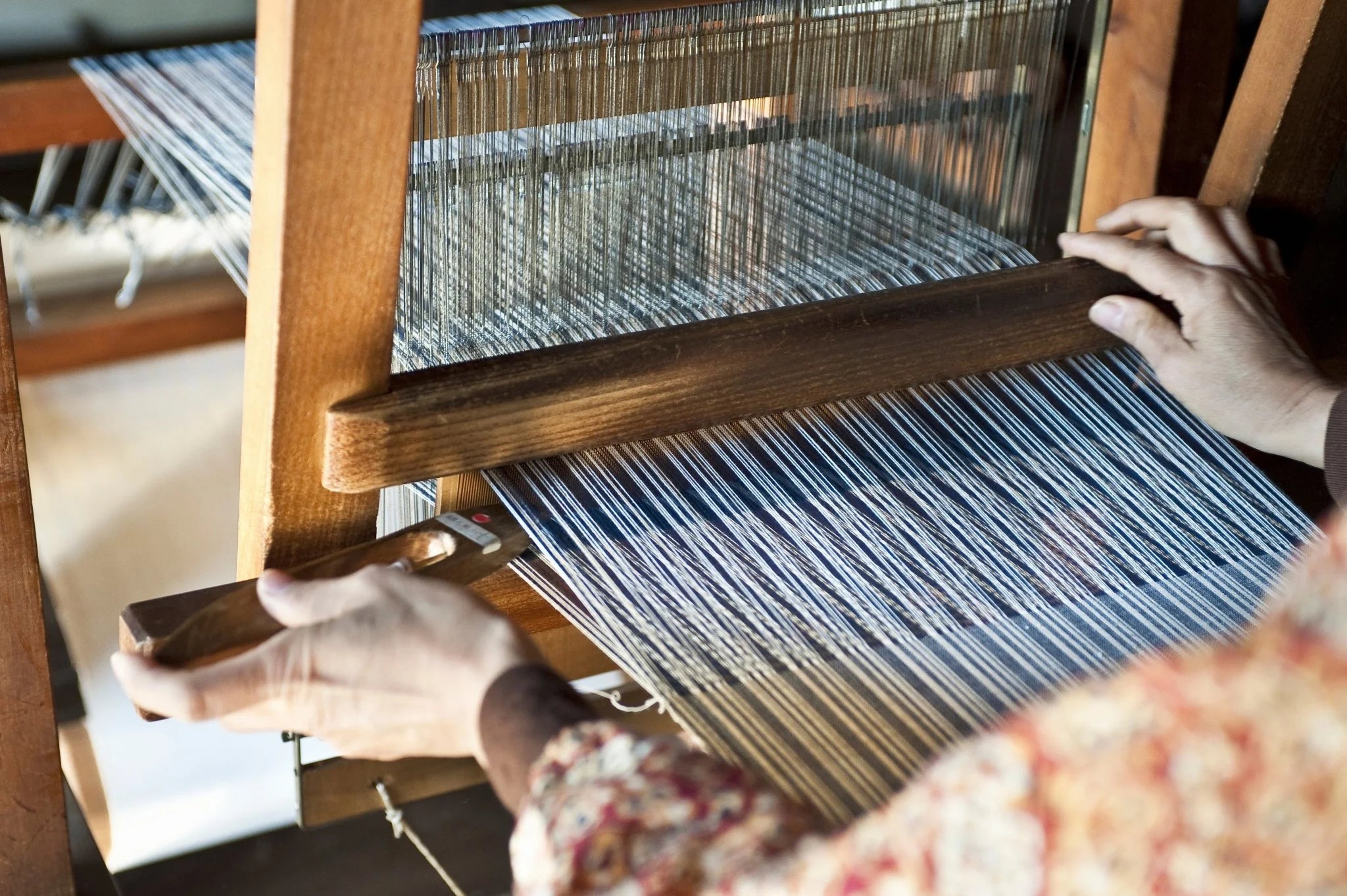
1. Designing
This is the most important process in Nishijin Ori.
Nishijin Ori use "yarn dyeing," in which fabric is woven from pre-dyed yarn, rather than "piece dyeing," in which the finished fabric is dyed. So it is necessary to plan a design that envisions the finished product. The designer receives an order from the manufacturer and creates a design that combines traditional patterns with contemporary demands.
2. "Monsho-Izu"
The next process is called "Monsyo-Izu", which is the process of making blueprints. The blueprints are made by projecting an enlarged design on a special sheet of paper similar to graph paper, then copying the pattern with a pencil and coloring along with the squares to show the combination of warp and weft yarns for the jacquard loom. In addition to yarn colors, various information and instructions designed to facilitate the weaving of the textile are also written on the paper.
3. "Monhori"
Monhori is a method in which holes are punched in a specialized paper called Monshi, and the information such as the position of warp and weft yarns and combination of colored threads drafted in Monsho-izu (blueprint) is specified one grid at a time. In order for the Jacquard loom to weave the pattern according to the information in the Monsho-Izu (blueprint), holes are accurately pierced using a machine called a piano-type Monhori-Ki. In recent years, computer graphic processing has also been used.
4. "Nenshi"
This process prepares the yarns to be woven into the Nishijin Ori. First, multiple silk threads are twisted together in a process called Nenshi, which First, multiple silk threads are twisted together in a process called Nenshi, which means "twisting threads," to adjust the thickness of the yarn. Twisting threads of various gauge gives the Nishijin Ori its unique three-dimensional texture.
5. Yarn Dyeing
The dyer refines the silk yarn to remove animal proteins that cause the yellowish tint, creates a pure white yarn, then dyes it in the color ordered by the designer. This process is an important step that determines the texture of the finished Nishijin Ori.
6. "Itokuri"
"Itokuri" is a process in which a skein of yarn dyed in the yarn-dyeing process is wound onto a yarn frame to prepare it for smooth work in the warping or horizontal winding process. In the past, the warp and weft yarns were wound manually, but nowadays, most yarn reeling is done by machine.
7. "Seikei" and "Nukimaki"
One of this process called "Seikei", is used to prepare the thousands of warp threads needed for weaving. The warp threads are threaded at a dizzying pace, and it is up to the fingertips of the skilled craftsman to find any defects in the warp threads. The other process called "Nukimaki", which is the weft yarns are spooled onto a bamboo tube, then inserted into a shuttle.
8. "Soukou"
Loop the warp threads through the Soukou (heddle) part of the jacquard loom. A Soukou is one of the parts of a loom that moves the warp threads up and down in order to pass the weft threads through the weft. Through this process, information on the structure and design of the textile is conveyed to the weaver.
9. "Tebata"
Weaving Nishijin Ori textile is done by handlooms called "Tebata", as well as by jacquard looms, power looms, and tapestry looms called "Tsuzure-bata". Although power looms have become most popular in recent years, some delicate textiles such as Kinran, woven with gold threads, must be made by hand on Tebata hand looms.
"Nishijin" in Nishijin Ori derives its name from the fact that weaving began at the site of the western military camp in Kyoto, which was the center of a civil war that engulfed all of western Japan in the 15th century.
However, even before the brand "Nishijin Ori" was established, the origin of textile production in Kyoto can be traced back to the 5th-6th century, when silk weaving technology was brought from the Asian continent. In the Nishijin area, the textile industry was already established in the Heian period (c.794-1185), which means that the history of the textile industry as a whole is more than 1,000 years old.
With the overwhelming support of the nobility and wealthy merchants, Nishijin Ori reached its golden age during the Edo period in the 18th century. Although the Nishijin area was almost destroyed by massive fires recorded in 1730, the introduction of Jacquard looms from France in the 19th century gave birth to the Japanese Jacquard weaving technique, which triggered the development of the Japanese textile industry.
With this breakthrough, Nishijin Ori became a world-class luxury silk brand in the 20th century, rivaling Lyon in France and Milan in Italy.
In 1976, Nishijin Ori was again recognized as a nationally designated traditional handicraft. With its superior weaving techniques and designs accumulated over more than 1,000 years, Nishijin Ori are fully demonstrating their value as artistic textiles even today, and will continue to pave the way for the future.
Makers
Filters