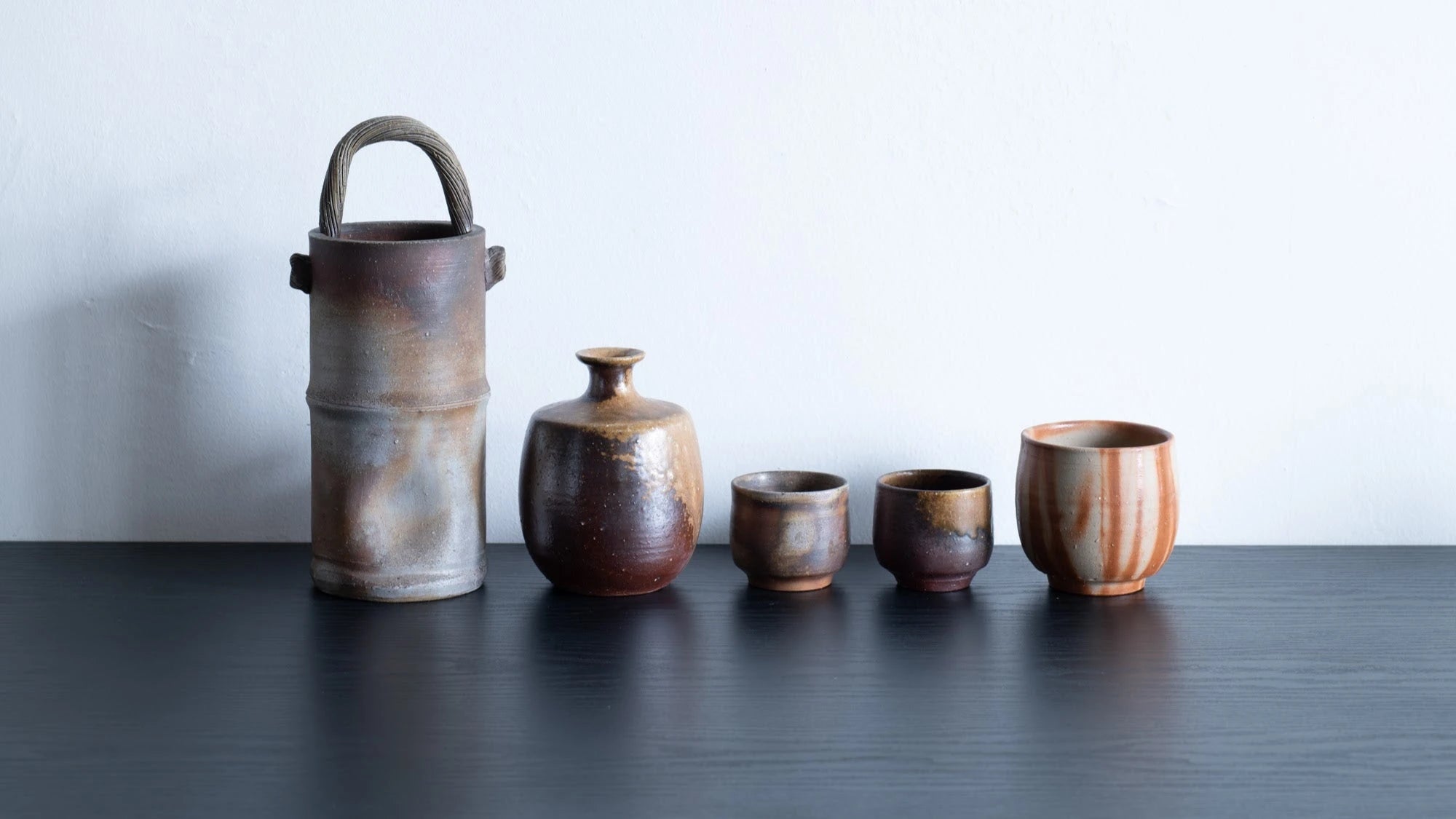
The Art of Clay and Fire
Bizen Ware
Bizen ware is a traditional stoneware produced in the Imbe area of Okayama Prefecture. It is one of the oldest ceramics in Japan, and is made using the yakishime technique, in which pieces are fired at high temperatures without glaze to make them durable and water-resistant.
Bizen ware is called "the art of clay and fire" for the exquisite colors and patterns produced by the kiln's flames, and is characterized by its minimalist, wabi sabi design.
Bizen ware is a special type of Japanese stoneware that continues to this day. The reason for this is a technique called "Yakishime," in which pieces are fired at high temperatures without glaze to add water resistance and durability. Bizen ware has been used to make jars, mortars, and other household items since around the Muromachi period (1333-1573), and it is said that "Bizen mortars are so durable that they will not break even if thrown," a saying that has come to be valued throughout Japan. In addition, the clay is well-fired and sturdy, and has sufficient water resistance without glazing.
In addition, Bizen ware has minute pores that allow a little air to pass through, so when sake, whiskey, or wine is placed in a Bizen ware jar, it is said to become more aromatic, mellow, and full-flavored. It is also said that this air permeability keeps water fresh, thus prolonging the life of flower arrangements.
Moreover, the charm of Bizen ware can be found most notably in its appearance. Bizen ware has a pattern called "Yohen", which is created by the flames of a traditional wood-fired kiln, and this is the reason why Bizen ware has the nickname "The Art of the Clay and Fire”, and is a supreme craft created by the knowledge and skill of Bizen ceramic artists with regard to the flames of the kiln.

Goma
This pattern is called Goma, because the pine wood used to fire the kiln turns to ash, which adheres to the work and gives it a pattern that looks like a sprinkling of sesame (=Goma) seeds.
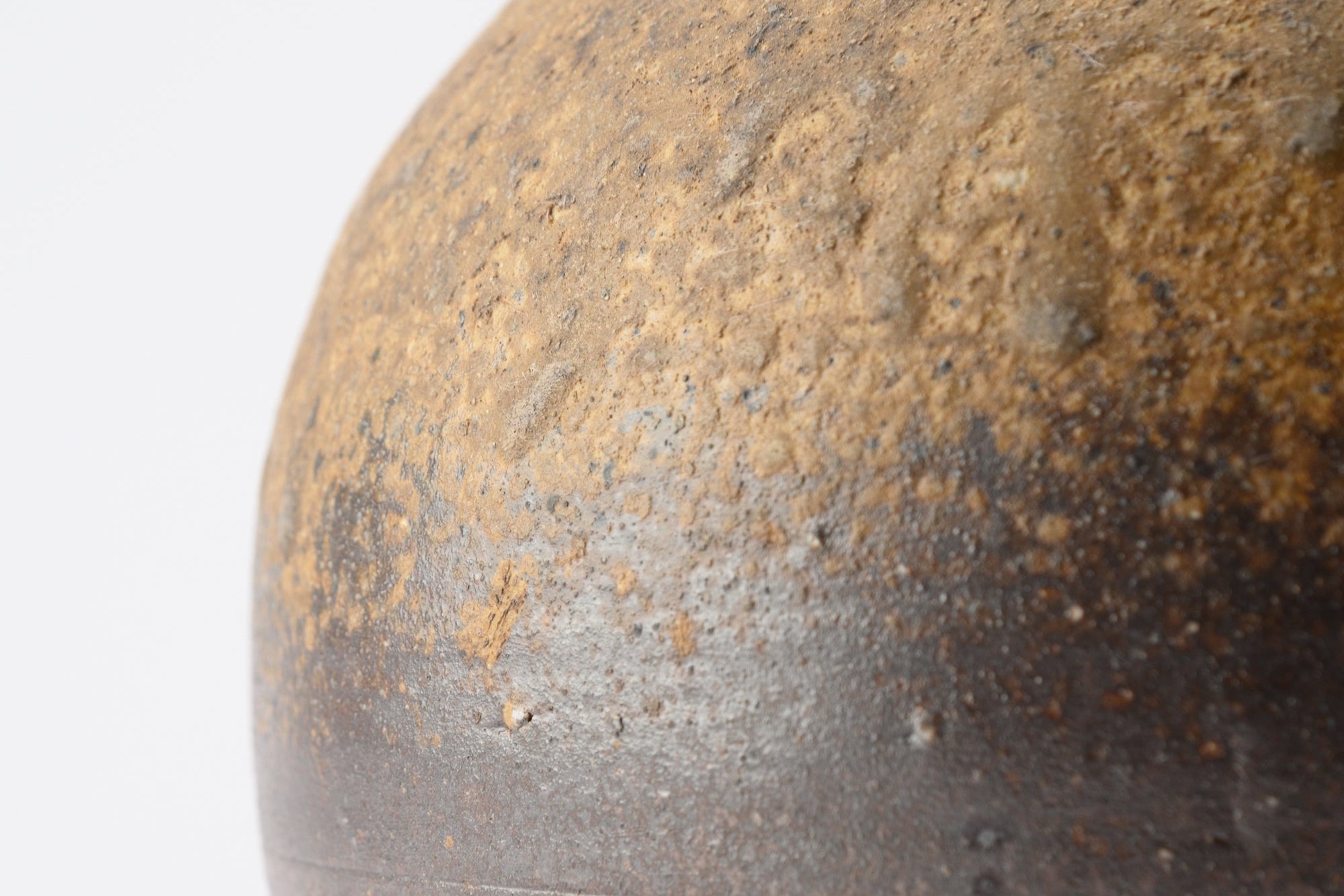
Sangiri
The "San" in Sangiri refers to the wall inside the kiln. The work placed on the side of the wall where ash tends to accumulate is covered with ash from the pine wood, and the part of the work not directly exposed to the fire reacts with the ash, turning it grayish brown or blackish brown.
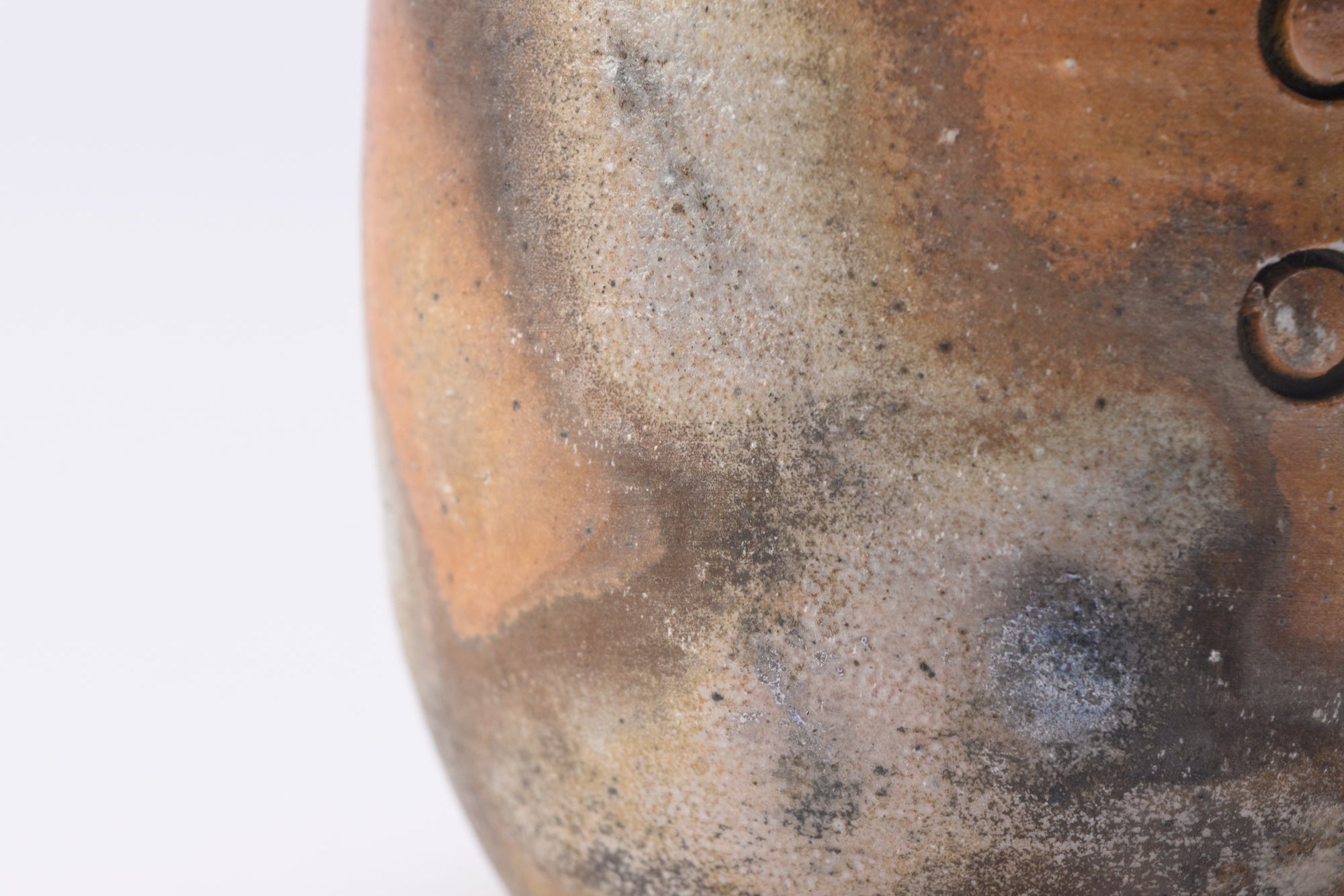
Hidasuki
This pattern is made when the work is wrapped in straw and placed in a kiln with a cover called a Saya, and fired in a place away from direct heat, it becomes light brown in color throughout and scarlet in the areas where the straw is wrapped. It is very popular because of the contrast between those vivid colors.

Botamochi
In order to prevent the works from sticking together, rounded pieces of refractory clay or small pieces are placed in between, which results in uneven firing, and the relevant areas turn lighter. The rounded shape looks like a Japanese sweets called botamochi, hence the name.
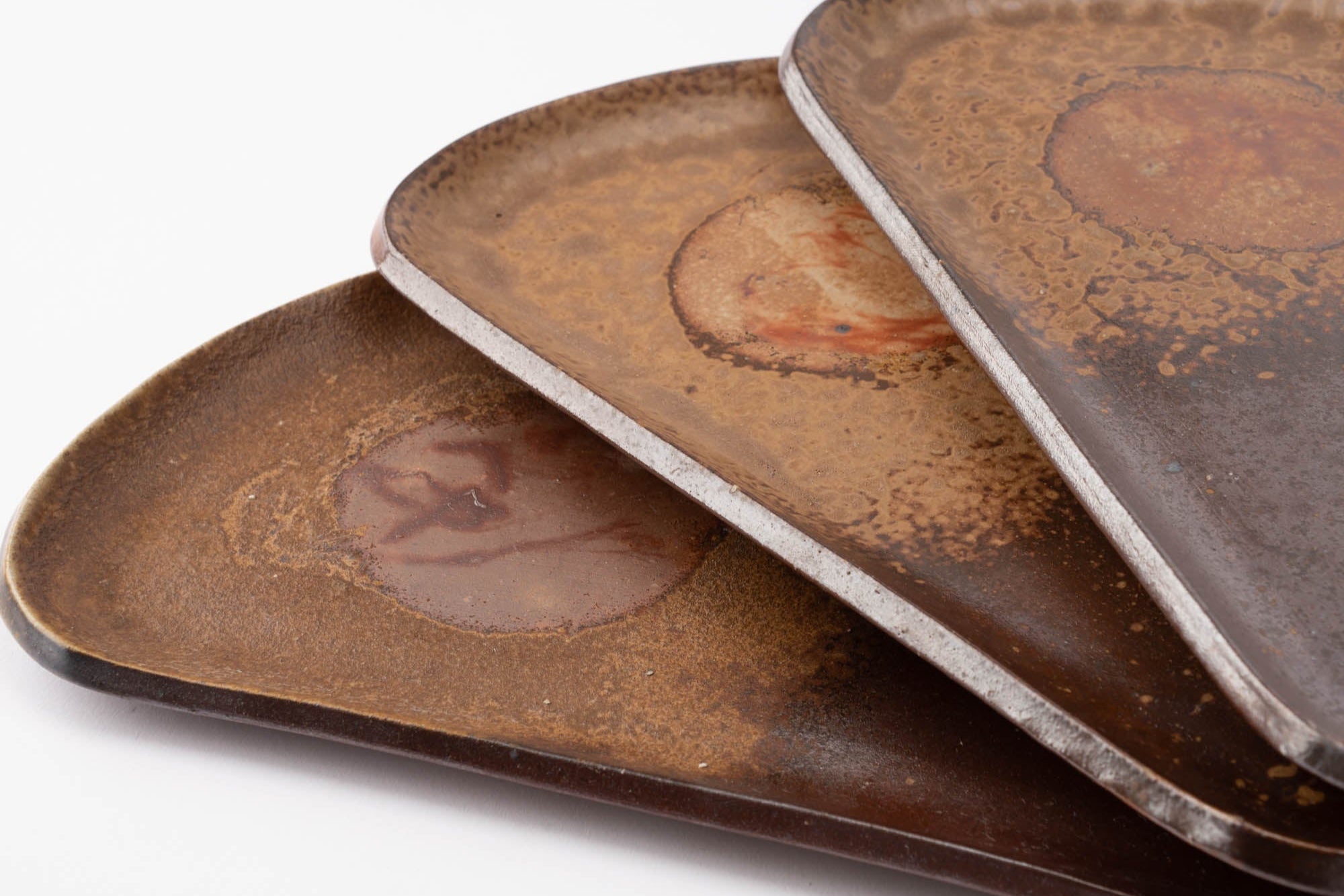
Bizen ware is stoneware that is descended from Sueki pottery, a hard, blue-gray colored earthenware produced in Japan during the Kofun period (about 300 to 538 AD).
It is said that the Sueki pottery production method was introduced to Japan via Korea. Around the 5th century, with the introduction of superior kiln and potter's wheel techniques from the Korean peninsula, it became possible to produce pottery with a more elaborate shape and finished at higher temperatures, and even unglazed Sueki pottery began to be used without water leaks.
The golden age of Sueki pottery was around the 7th century, and in the area straddling Setouchi City and Bizen City, there are still remains of workshops and kilns where Sueki pottery tiles and daily utensils were made, called "Oku Old Kiln Sites". The pottery industry continued there for nearly 100 years, but when clay and other resources were depleted, their potters moved north area of Bizen City in search of more resources. The new kiln industry that began there is the origin of Bizen Ware, a tradition that continues to this day.
In the early Kamakura period (1185–1333), Bizen ware began to be produced in the same style as today's Bizen ware. This early Bizen ware is called “Ko-Bizen" and is highly valued as an antique.
In the Sengoku period (1568-1600), the philosophy of the tea ceremony, which was making great strides at that time, matched the simple beauty of Bizen ware, and those tea utensils came to be valued in the tea ceremony. Since that time, six of the main Bizen ware potters, Kimura, Kaneshige, Mori, Ohae, Tongu, and Terami, were encouraged to produce Bizen ware under the protection of the Bizen clan, and they continue the oldest Bizen ware tradition.
Today, Bizen ware is a simple yet sophisticated stoneware that captures the spirit of the tea ceremony, and in 2017, it was designated as one of the Six Ancient Kilns, a Japanese Heritage Site.
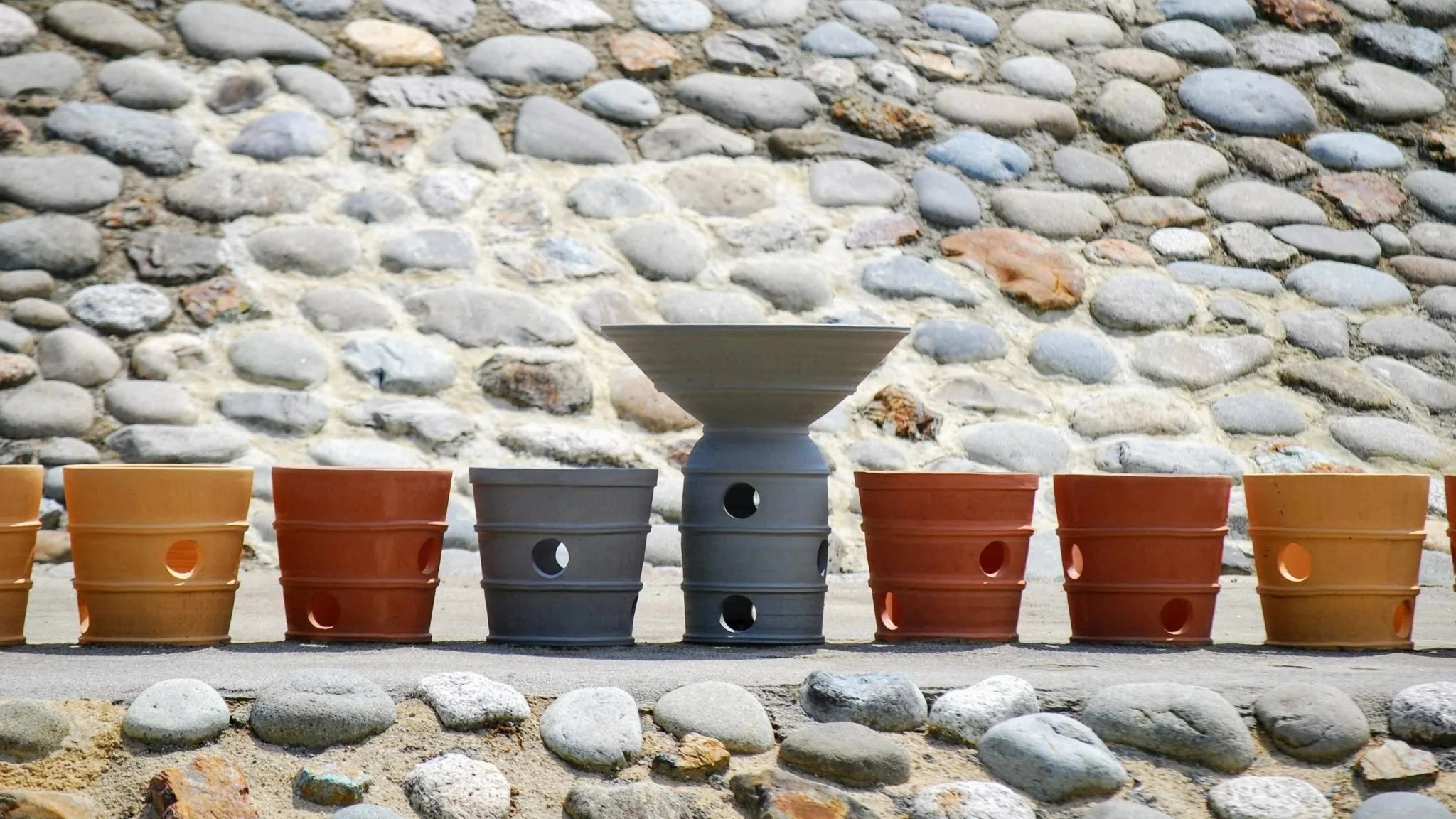
What About "Yakishime"?
Yakishime, also known as Shime-Yaki, is a Japanese stoneware firing technique used to make Bizen ware. By firing without glaze for a long period of time at a very high temperature of about 1300 degrees Celsius (2372 F), the glass component in the clay melts and fills the spaces between the clay particles, creating a strong and solid material that is also highly water resistant.
Bizen ware made with Yakishime is also slightly breathable, which makes water in tablewares less likely to spoil, improves the taste of sake, and mouthfeel of beer and other sparkling drinks. Simplicity of the clay itself, and its unique moist luster stimulate a contemporary sense of beauty.
Preparation of Clay / Forming
The clay used for Bizen ware is called Hiyose, which is dug out from the fields around Bizen City. The clay is exposed to wind and rain for 1~2 years after collection, then ground with a mortar, and elutriate to extract only the finer and smoother clay. Then the fine clay is left to settle for a few weeks to a few months, then mixed with black clay and left to settle again for another six months to a few years before it is finally ready for use as potter's clay.
Bizen ware is formed in the same way as other pottery, but because it is unglazed, it is easier to judge the quality of the form and requires a high degree of precision in its formation. Decoration is kept to a minimum in order to bring out the Yohen pattern, but sometimes a spatula is used to create decorations, or the clay is scraped off to create angles.
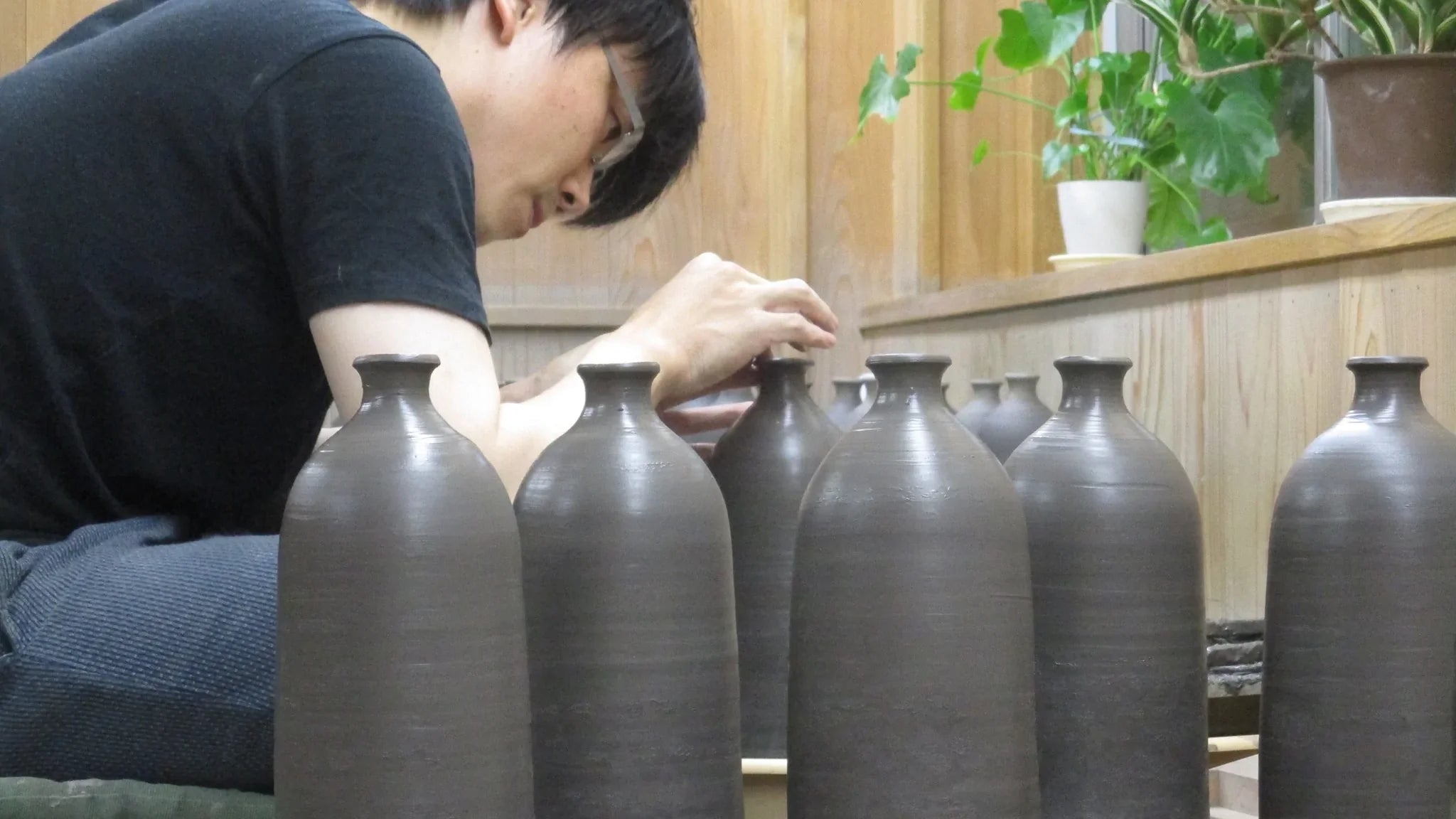
Firing Process / Finishing
Unlike Arita ware and Kutani ware, which are fired several times with different temperatures in different processes, Bizen ware is fired only once.
Bizen ware is usually fired in a climbing kiln, using red pine firewood as fuel. The kiln is first fired with a small amount of firewood, gradually removing the moisture from the works and raising the temperature little by little, until finally a large amount of firewood is fed into the kiln and the temperature is raised to about 1300 degrees Celsius (2372F).
This kiln firing process takes from one week to ten days, and is a very large-scale operation that is carried out day and night. During the firing process, ash and straw adhere to the works, creating a unique Yohen pattern which gives each piece in the kiln a richly expressive appearance.
By arranging pieces of different sizes, figuring out the passage of the flame and loading them into the kiln, a flow of flame is created and a variety of different expressions can be created. The pattern is not created by accident by the flames of the kiln, but by the artist's intention during the kiln firing process.
Bizen ware firing is one of the most important shows of skill for Bizen ware artists, and is the reason why Bizen ware is called "the art of the flame".
After being removed from the kiln, the works are polished by the artists and carefully inspected before being sent to the market. Each Bizen ware work is a unique piece of art, with no two pieces having the same Yohen pattern, even if they have the same shape.
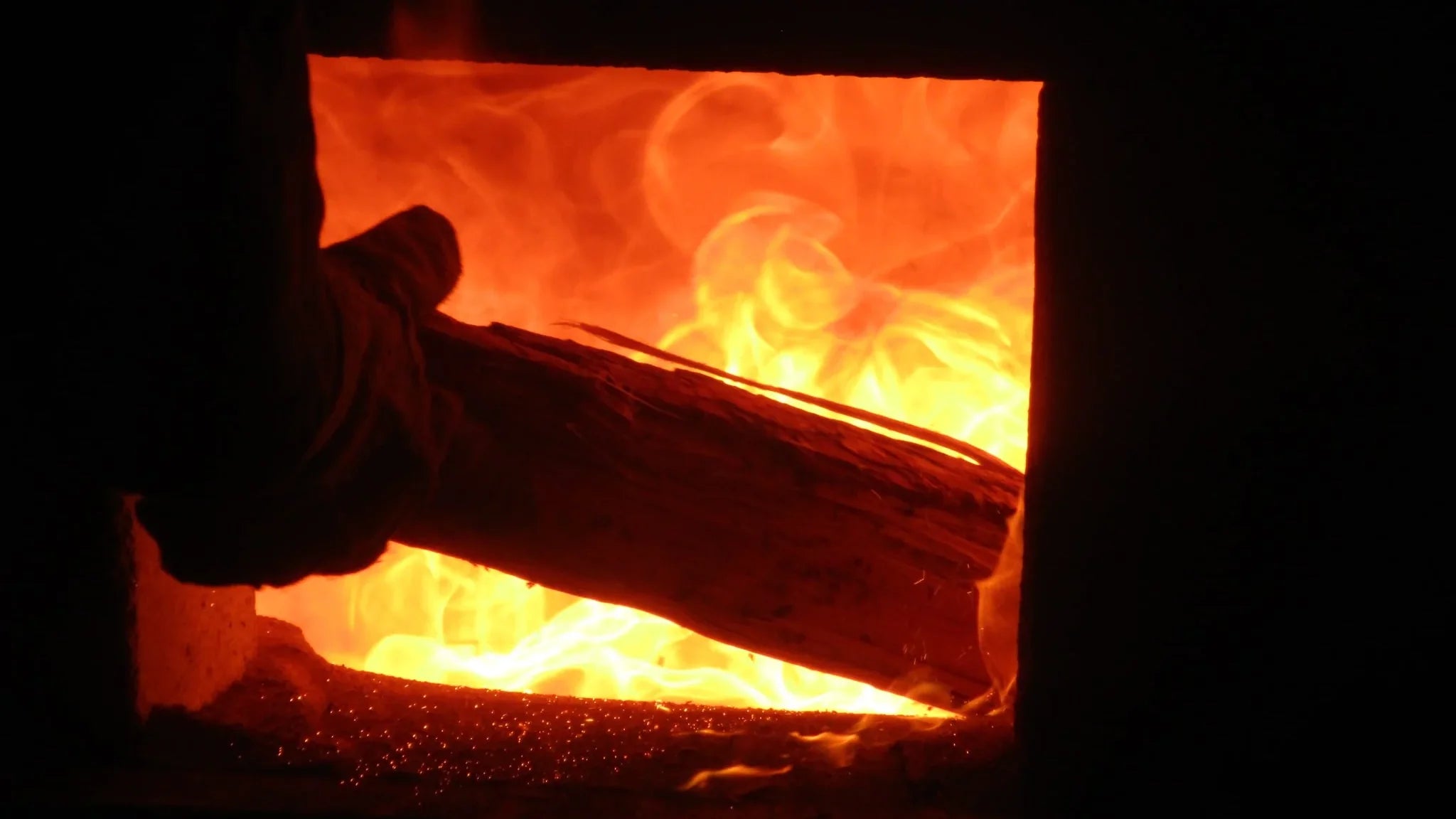
Related posts

7 Actually Useful Table Accessories That You Didn’t Know You Needed
Discover 7 unique Japanese table accessories, from soy sauce dispensers to spice holders, that add charm to every meal.
Read more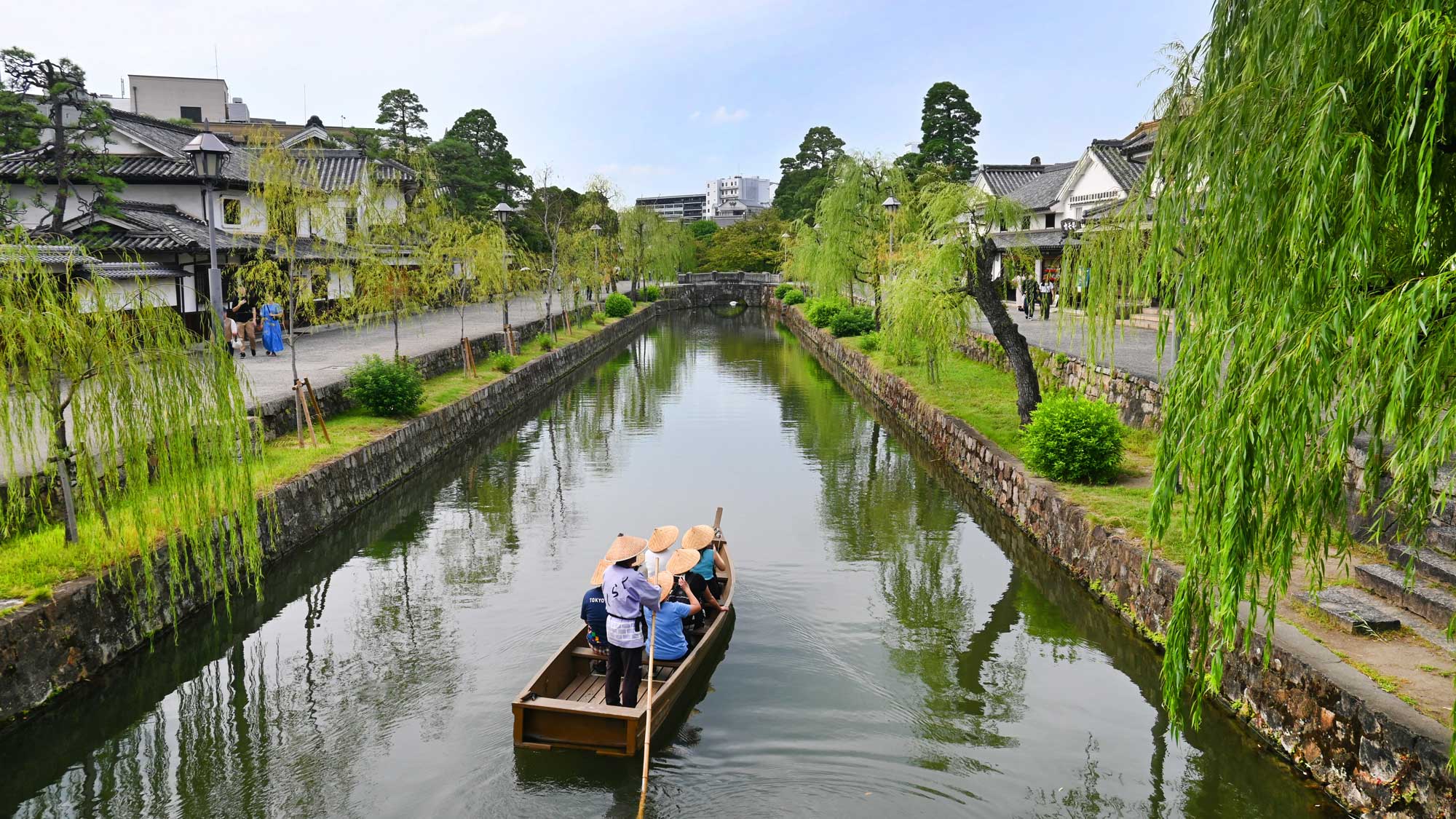
Early Summer Escape: Travel Through Tableware
Travel Japan through tableware this summer. Explore handcrafted pieces from Kyoto, Tokyo, Akita, and more.
Read more
Dobuchi Yoshiaki: Decoding the Secrets of Yohen Tenmoku
Uncover the mystery of Yohen Tenmoku, a lost ceramic art of cosmic beauty, revived by Dobuchi Yoshiaki.
Read more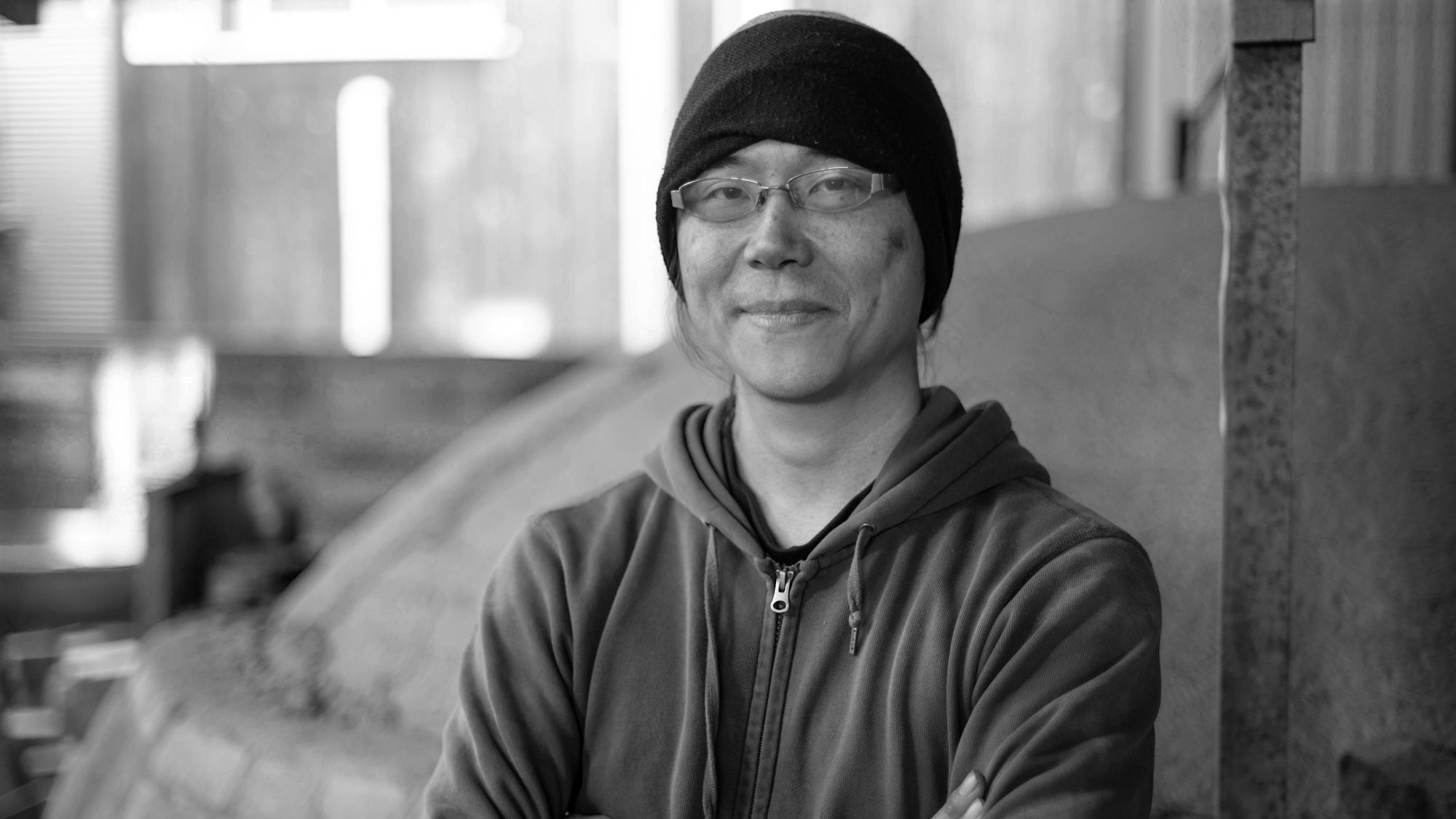
Mori Toshiaki's Journey in Reimagining Bizen Ware
Learn about Bizen ware artisan Mori Toshiaki, and his unique forms, experimental firing, and a bold vision for the future.
Read moreFilters