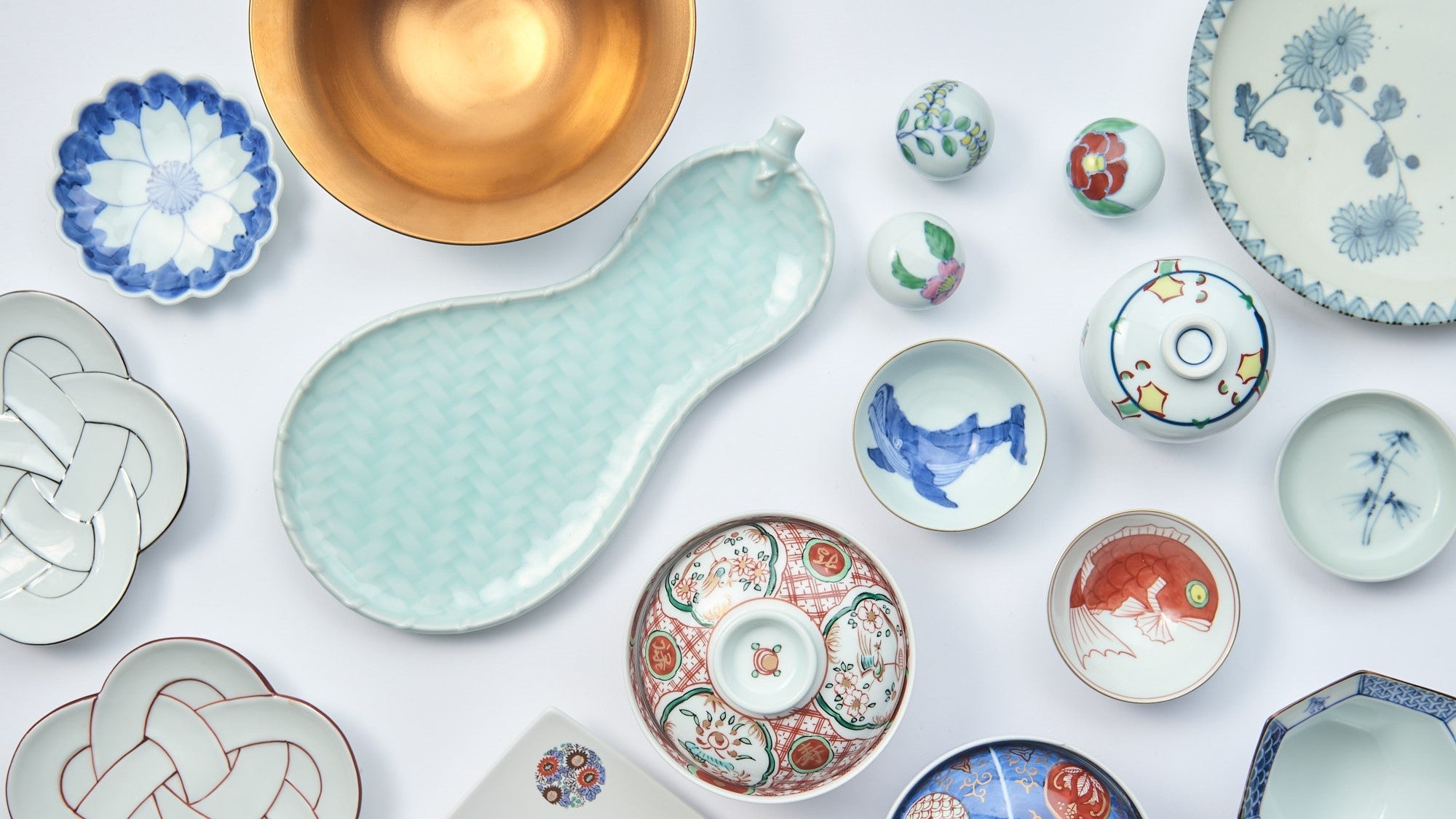
Arita Ware
Crafted in the historic town of Arita, located in Saga Prefecture, Arita ware stands as the most venerable porcelain production hub in the annals of Japanese history. Characterized by its ethereal translucent white surface adorned with vibrant paintings, it has profoundly influenced the porcelain craft across Europe.
Within Japan, Arita ware is held in high esteem as a prestigious brand, with the town of Arita acknowledged as a quintessential production area.
Arita ware is considered Japan’s premier porcelain, boasting a 400-year history. Its production relies on a specialized division of labor—ranging from clay refining and forming to painting and glazing—which has fostered a high level of craftsmanship at every stage, resulting in top-quality products.
Arita ware is primarily crafted using a unique pottery stone known as Amakusa pottery stone. Prized for its inherent whiteness, this stone imparts qualities that make Arita ware exceptionally light, thin, and resistant to breakage. When held up to sunlight, the ware’s translucent surface further attests to the remarkable properties of this special material.
A wide range of glazing techniques is employed in Arita ware, from sometsuke underglaze—using a deep blue pigment called gosu—to kinrande overglaze, featuring vibrant hues of gold, red, and blue set against a crisp, beautifully white porcelain backdrop.
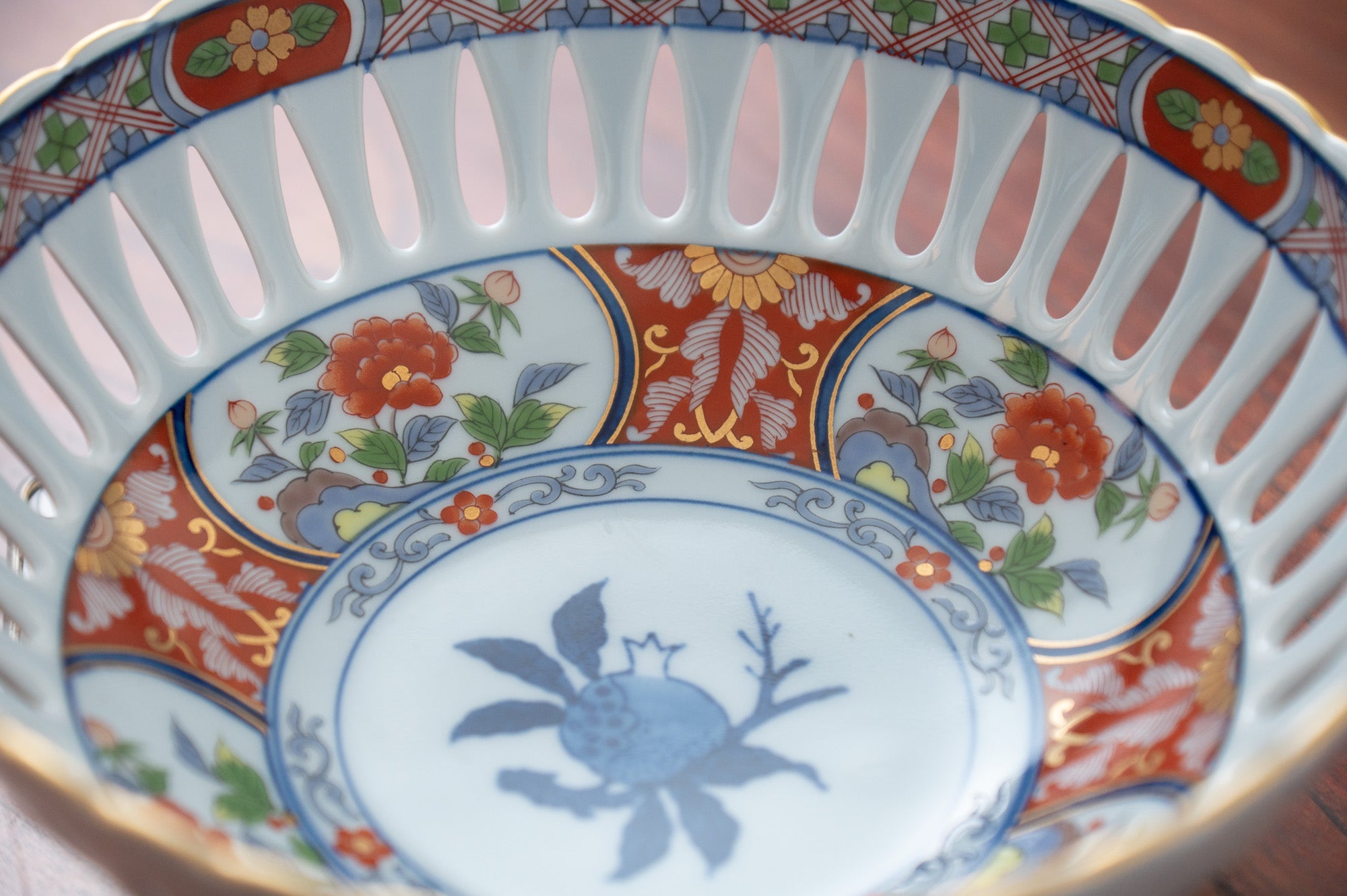
The Origins of Arita Ware
Japan’s oldest porcelain, Arita ware, was created in the early 17th century by Korean craftsman Yi Sam-Pyeong, known in Japan as Le Sanpei (or Ri Sanpei). He was brought to Arita by Nabeshima Naoshige, the lord of Saga, and was supported by the influential Taku family.
Yi Sam-Pyeong initially struggled to find suitable raw materials for porcelain production. Around 1610, he discovered high-quality pottery stone at Izumiyama in Arita. By 1616, he successfully fired porcelain and presented it to Lord Nabeshima, marking the official beginning of Arita ware.
In recognition of his achievements, the Taku family gave him the Japanese name Kanagae Sanbee. However, his descendants continued to use the name Yi Sam-Pyeong, a tradition that remains today.
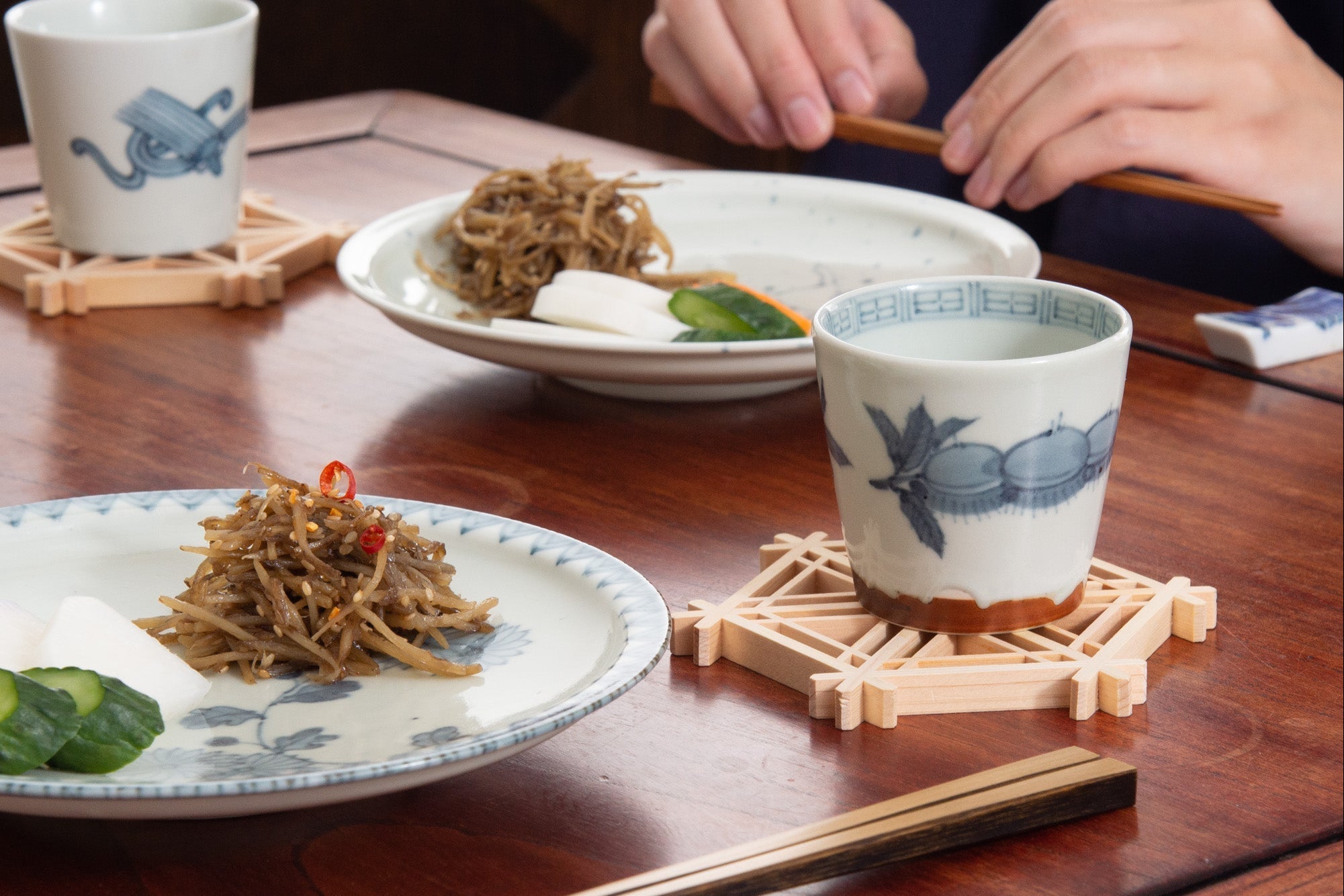
From Imari Ware to Arita Ware
At the time, China dominated porcelain trade. However, after the fall of the Ming Dynasty (1368–1644 CE) and the decline of Jingdezhen porcelain production, the Dutch East India Company (VOC) sought new sources and turned to Arita. The products were exported through Imari Port, becoming globally recognized as "Imari ware."
From the 1650s, the VOC began exporting Imari ware to Southeast Asia and Europe. As Europe lacked the technology to produce porcelain like China or Arita, owning porcelain became a status symbol among European royalty. The white porcelain of Imari ware was referred to as "White Gold" and became a prized item in aristocratic collections. It also greatly influenced European porcelain makers, including Meissen.
Until the late Edo period (1603–1868 CE), Arita was Japan’s only porcelain production center. However, a devastating fire in the Arita Sarayama district destroyed much of the town. During the Meiji era (1868–1912 CE), Arita recovered by inviting foreign potters, studying porcelain science, and refining its techniques, reviving its export trade. In 1897, the opening of a railway to Arita helped popularize the name "Arita ware."
Despite periods of decline, Arita ware’s craftsmanship was preserved and passed down through generations. In 1977, it was officially designated as a Nationally Recognized Traditional Craft of Japan.

1. Forming
Porcelain ore and ceramic stone are refined into porcelain clay and formed using a potter's wheel or plaster mold. The porcelain ore used in authentic styles such as early Imari is Izumiyama porcelain ore, but most of the current Arita ware uses Amakusa pottery stone from Kumamoto Prefecture.
2. Shaping
In the process of creating ceramic vessels, shaping is the most crucial step. While the specific technique depends on the type of ware, its intended use, and its functionality, there are two major methods: wheel throwing and slip-casting. Arita ware primarily utilizes the wheel-throwing technique.
3. Bisque Firing
The dried base is placed in a kiln and fired at a temperature of about 900℃ (1652℉). Bisque firing will prevent damage in the subsequent steps.
4. Underglazing
Underglaze decorations are painted on with a pigment called gosu, which is used to paint items in different shades of blue, from pale blue to dark blue, such as sometsuke. In addition to blue, gosu in its black form is used to outline colorful styles like kinrande.
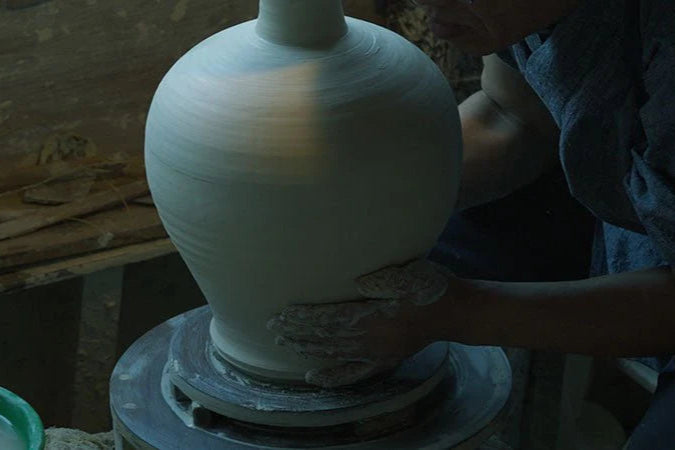
5. Glazing
Each Arita ware kiln applies a uniquely formulated glaze, which results in a smooth, transparent, glassy coating after firing. This completes the underglaze process.
6. High Firing
Firing is done at a high temperature of about 1300℃ (2372℉). Many kilns now use electric kilns, but traditional kilns such as the Ri Sanpei Kiln sometimes use natural wood-fired kilns. Underglaze work, such as sometsuke, is completed at this point.
7. Overglazing
The overglazing process seen in styles such as kinrande, Kakiemon and Nabeshima is done after high firing. Red, green, yellow, gold, silver, and colors other than gosu blue are used for the overglaze. There are two types of Arita ware painting: hand-drawn and stenciled, with the hand-drawn pieces considered more valuable as works of art.
8. Final Firing
After the overglazing, the pieces undergo a final firing at approximately 720–830℃ (around 1328–1526℉), completing the Arita ware production process.
Photos by Saga Ceramics Industrial Association.

Related posts
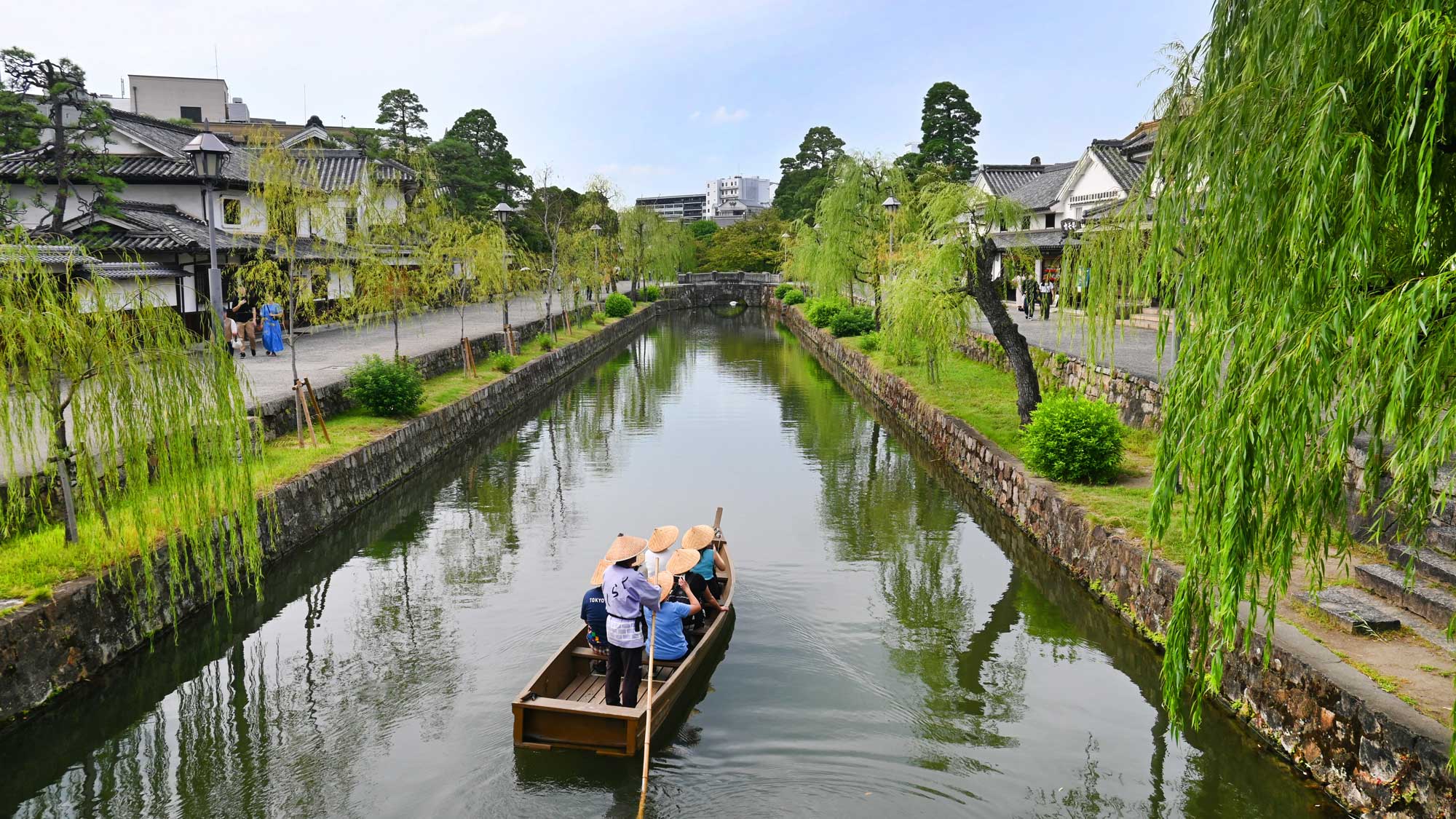
Early Summer Escape: Travel Through Tableware
Travel Japan through tableware this summer. Explore handcrafted pieces from Kyoto, Tokyo, Akita, and more.
Read more
A Tea Table in Bloom: Arita Ware and Seasonal Sweets
Set the scene for tea time with Arita ware, kabazaiku, and Kyo ware, savoring seasonal sweets and timeless craftsmanship.
Read more
The Legacy of the 14th Generation Master at Le Sanpei Kiln
At Le Sanpei Kiln, 14th-generation master Kanagae Sanbei keeps Arita ware’s traditions alive with a rare climbing kiln.
Read moreFilters