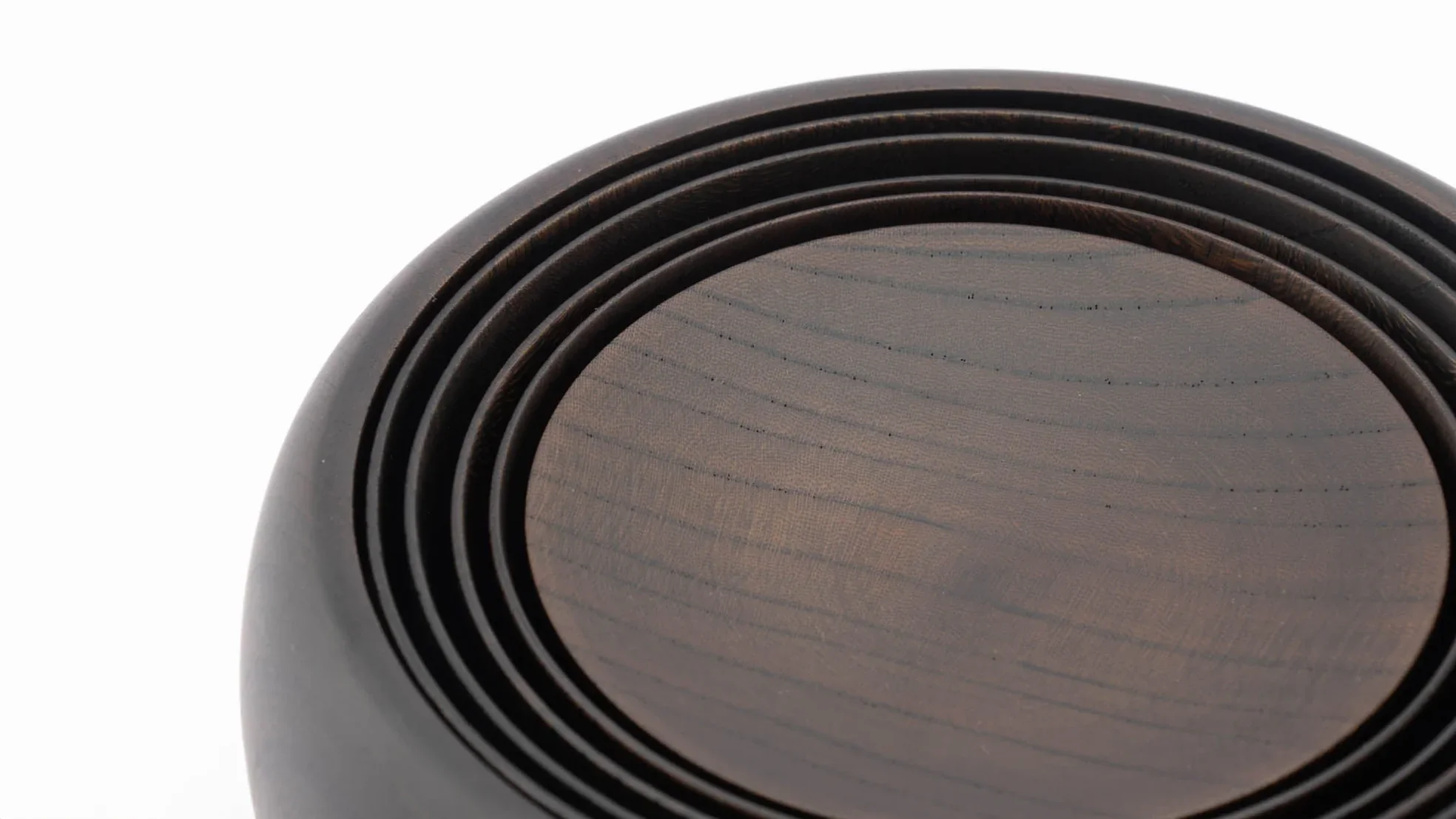
GATOMIKIO
GATOMIKIO is a brand name of company GATO MIKIO SHOUTEN, a specialist in Japanese woodworking techniques. They are especially skilled in bringing out the beauty that only natural wood grain can have. Their concentric-circle carving results in striking silhouettes.
Never compromising on quality of materials, precision of wood turning, or clarity of lacquer, GATOMIKIO creates pieces that are at once elegant, long-lasting, and functional.
GATO MIKIO SHOUTEN was originally founded as Gato Sawmill in 1908 in Yamanaka Onsen, a town famous for wood turning. Following the spirit of the original wood turners, they continue to aspire to woodworking perfection, with pieces completed individually by craftspeople.
Related posts
Filters