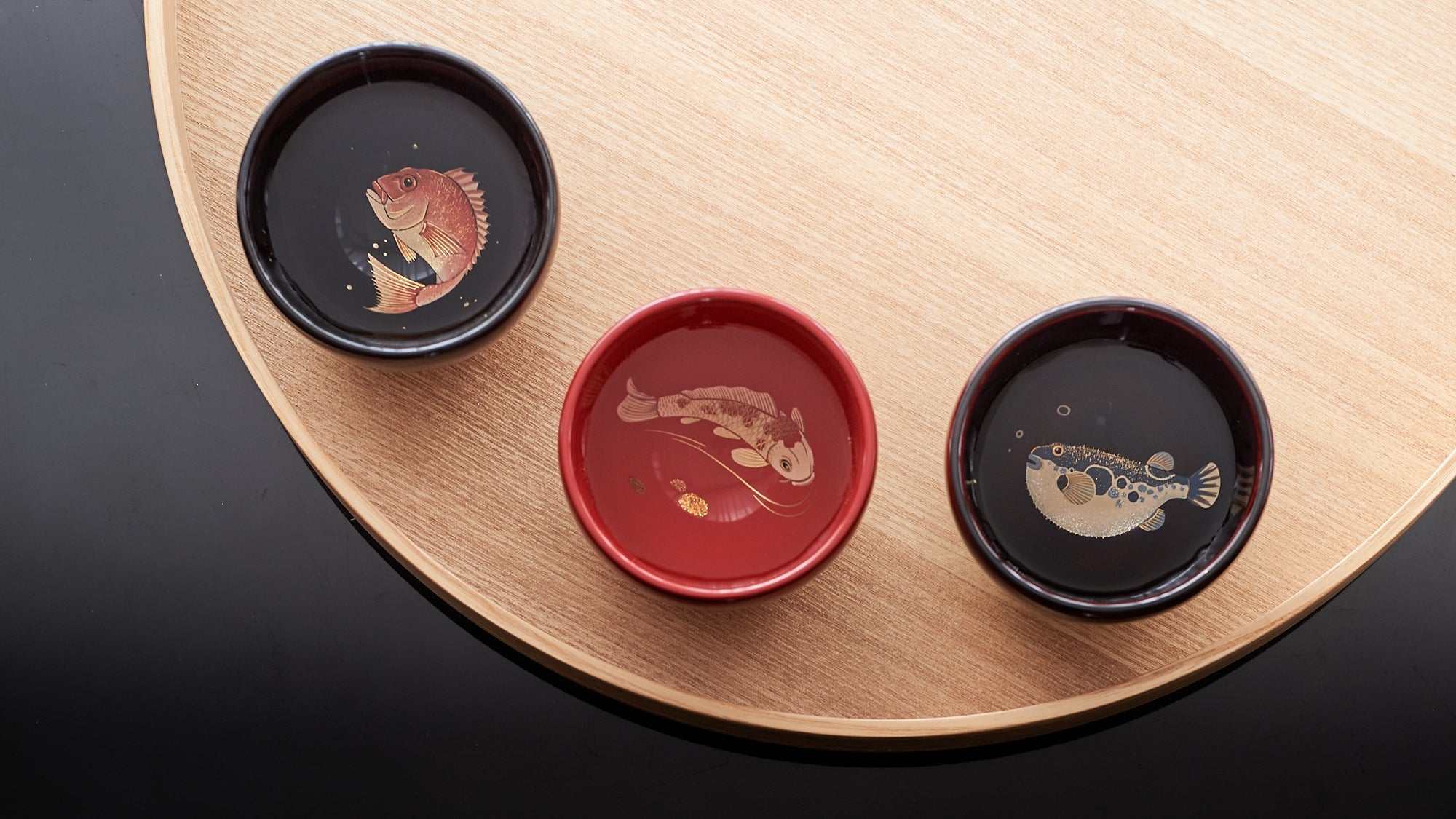
Enduring Beauty and Timeless Richness
Wajima Lacquerware
Wajima lacquerware, one of Japan's most esteemed lacquerwares, finds its home in Wajima City, nestled in the northwest corner of the Noto Peninsula. This illustrious craft, flourishing since the Edo period (1603 CE–1868 CE), is distinguished by its rich foundation and decorative embellishments that promise both aesthetic and functional excellence.
With an astounding number of steps in its production process, its sumptuous lacquer coat and exquisite decorations draw one into the mesmerizing world of Wajima artistry. Honored as an Important Intangible Cultural Property in 1975, Wajima lacquerware gracefully continues its evolution while maintaining the rich tapestry of its ancient traditions.
Division of Labor
One of the distinctive features of Wajima lacquerware lies in its highly specialized division of labor within its manufacturing process. Composed with over 100 detailed steps, each one is carried out by skilled artisans specializing in specific tasks. For example, Kiji-shi (wood turners) craft the wooden base, and nuri-shi (lacquer masters) apply the lacquer coating. This level of specialization is a testament to the pursuit of durability and beauty.
Stringent Artisanal Standards
Inheriting the legacy of their forebears, the Wajima Lacquerware Cooperative Association has set forth strict guidelines for the manufacturing process. These standards guarantee that only products crafted through traditional methods using wood, natural lacquer, and jinoko sourced from the Wajima mountainsides are recognized and certified as authentic Wajima lacquerware.
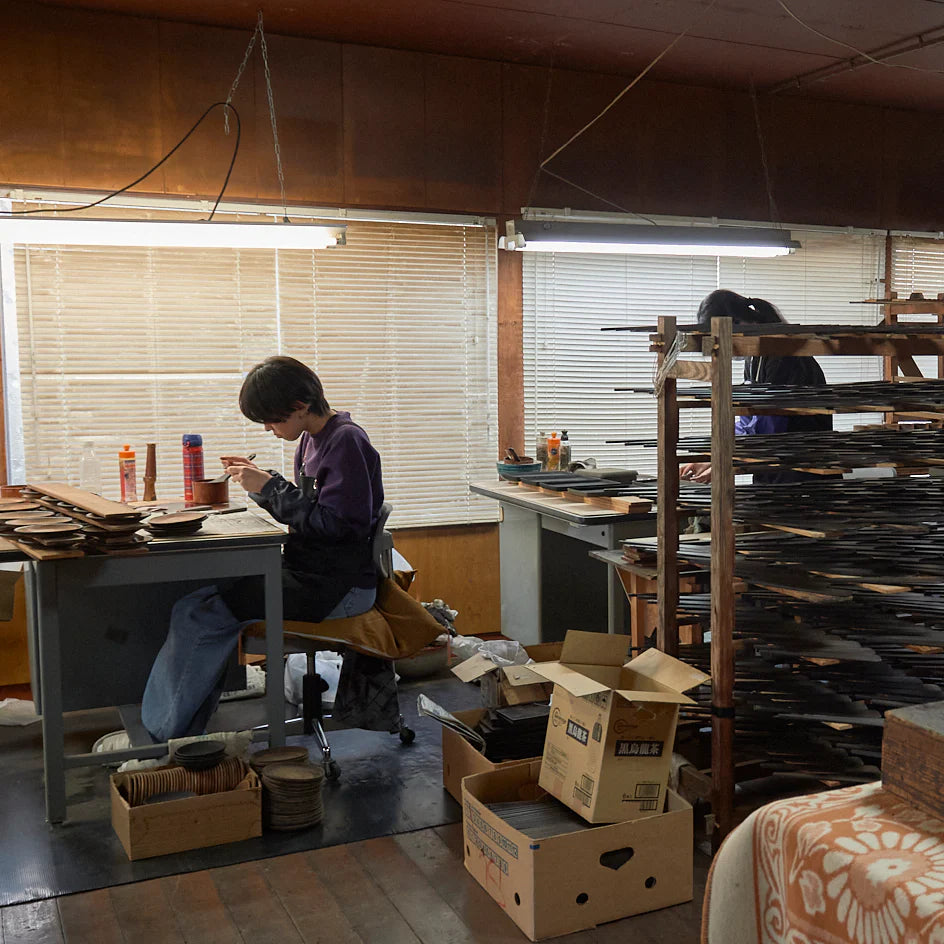
Sustainable Elegance
Lacquerware production employs entirely natural materials and tools. The durability of these lacquerware items ensures long-lasting use, contributing to resource conservation. Furthermore, at the end of their lifecycle, these products biodegrade and return to the earth. The lacquer itself dries upon exposure to natural air, adding an additional layer of environmental safety.
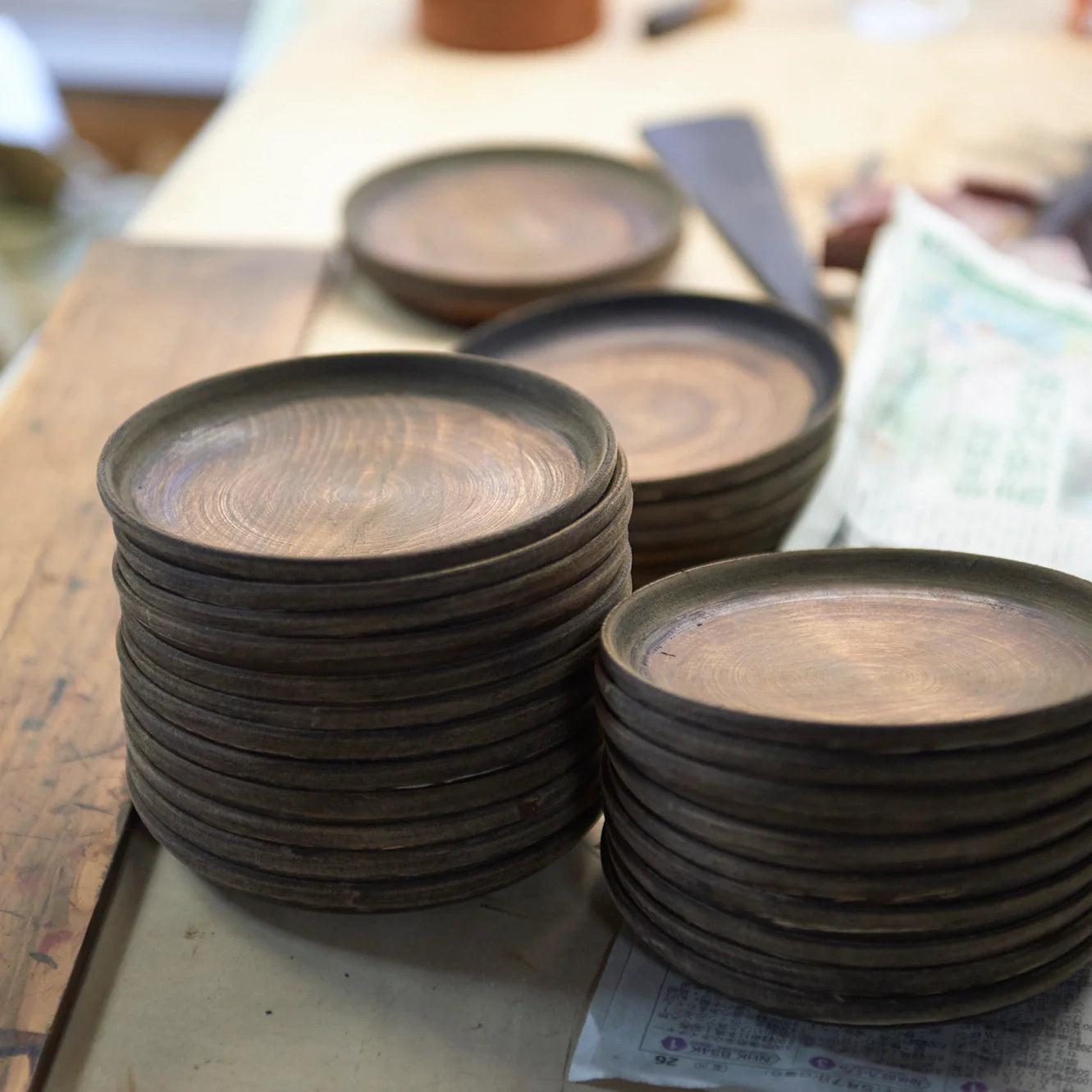
The history of Wajima lacquerware stretches deep into the past, with its earliest known artifact being a Japanese-style lacquerware door from 1524. This piece, preserved at Juzo Shrine in the heart of Wajima City, stands as the oldest example of Wajima lacquerware. Yet, its origin remains shrouded in mystery, surrounded by various theories.
The masterful style of Wajima lacquerware, as revered today, has its origins in the early Edo period.Jinoko, a unique diatomaceous earth from Wajima's mountainous regions, was adeptly integrated into the base coat, giving the lacquerware its distinctive thickness and durability. This pivotal discovery coincided with the Kaga Domain's era of artistic patronage, enhancing Wajima lacquerware's prominence. The domain's commitment to cultural development nurtured various crafts, turning Wajima lacquerware into a symbol of sophistication and prestige.
As the Edo period advanced, the artistry of Wajima lacquerware was further refined with the introduction of thechinkintechnique and maki-etechnique. Both decorative methods bestowed upon Wajima lacquerware an additional layer of beauty, enhancing its luxurious and esteemed characteristics.
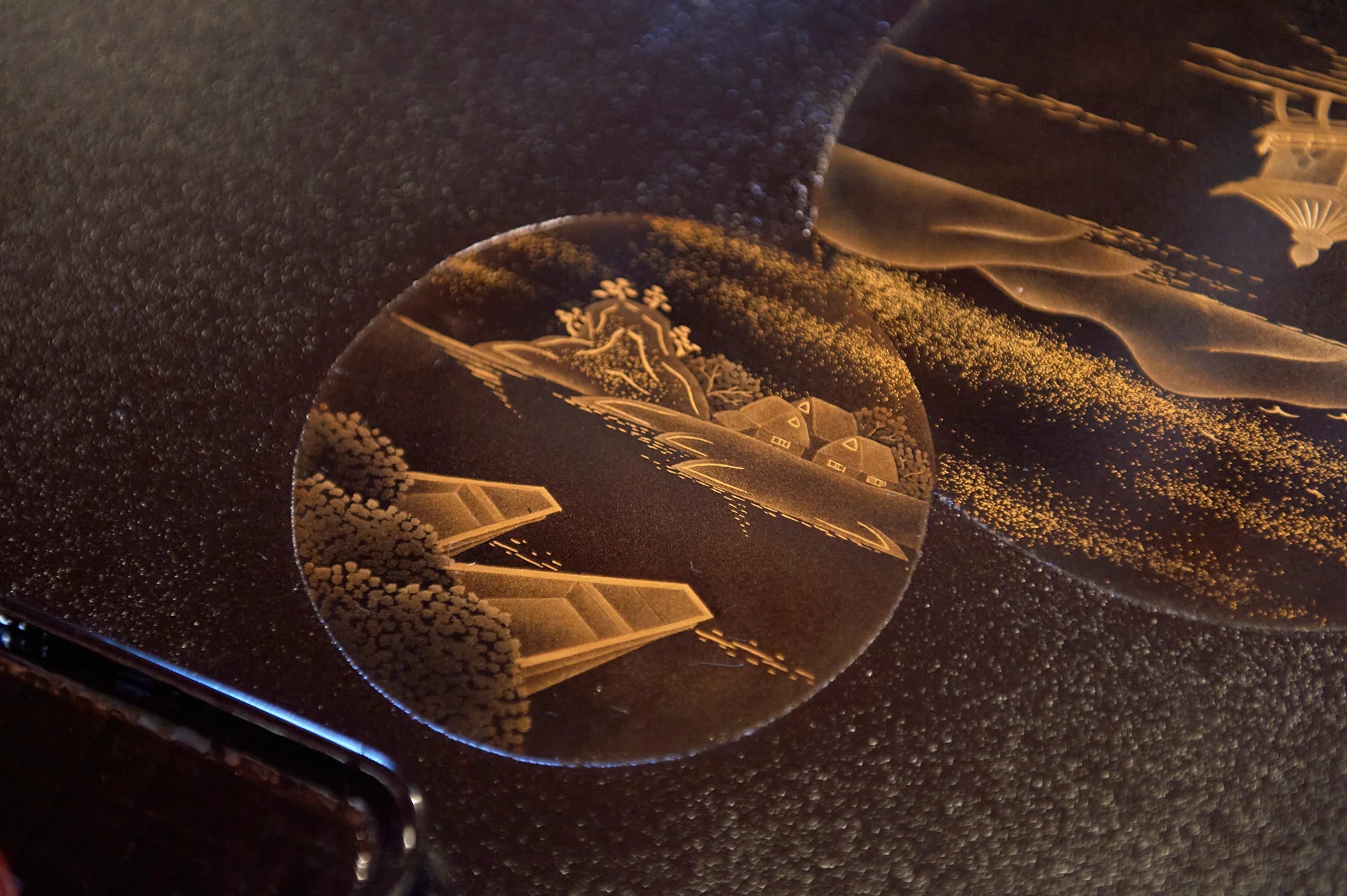
The production of Wajima lacquerware is structured around a specialized division-of-labor system. Over 100 intricate steps, each executed by expert artisans, contribute to its high quality. This meticulous crafting process, often extending beyond six months for each piece from its wooden base, ensures unparalleled attention to detail and depth of craftsmanship. The production process can be primarily categorized into the following with each inclusive of multiple precise steps.
Wood Base Preparation
Kiji-shi artisans masterfully sculpt the base using locally sourced, fine woods.
The process begins with segmenting a log into sections, which are then initially carved, slightly larger than the final product's dimensions. This roughly carved base is dried for about a year to prevent warping and cracking in the completed lacquerware. After this drying period, it is mounted on a lathe and intricately shaped inside and out, crafting the final piece.
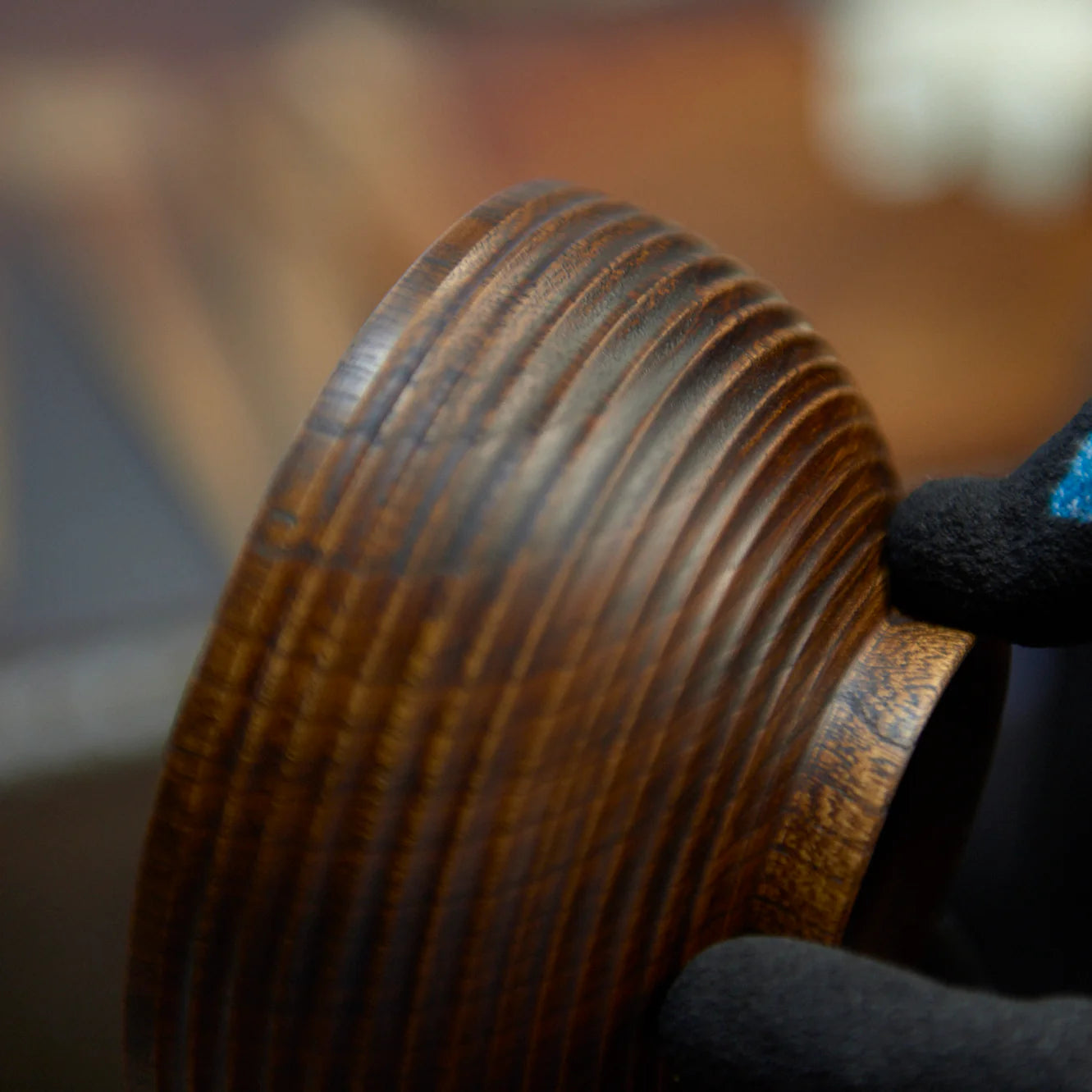
Base Coating
The detailed process of applying the base coat amplifies Wajima lacquerware's enduring quality.
The inaugural step in the creation of Wajima lacquerware is the delicate nuno-gise, or "cloth attachment" process. Fragile sections of the wooden base are reinforced with fine fabric, adhered using a blend of raw lacquer and rice paste. Following this foundational step, skilled artisans apply multiple coatings of jinoko-infused lacquer, utilizing specialized spatulas. Upon the drying of the third and final coat, the surface is then refined with a series of whetstones, to achieve a flawless finish.
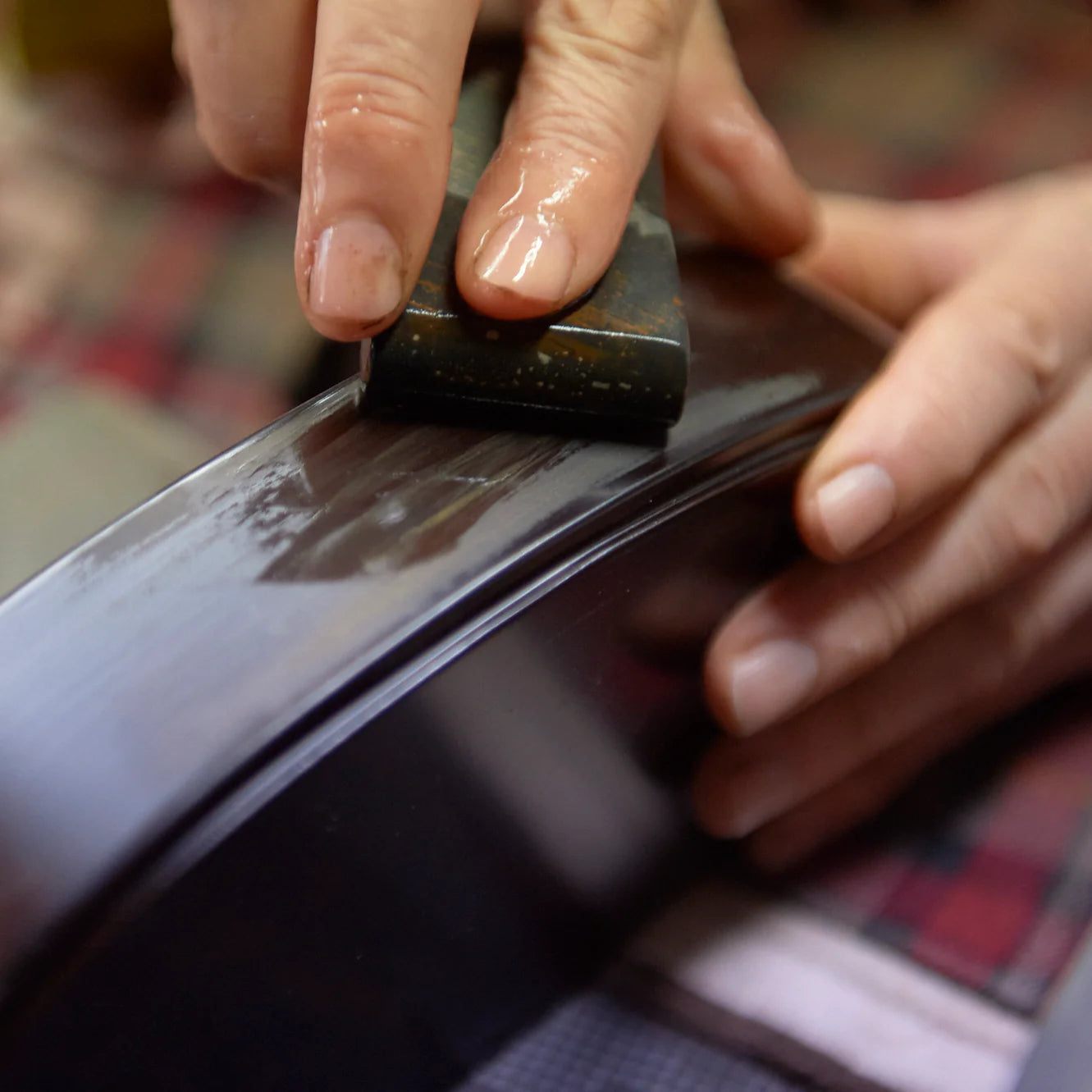
Lacquer Coat Finish
A subsequent high-purity lacquer layer is evenly applied as a mid-coat before the finishing layer. Considering the sensitivity of lacquer to environmental conditions, artisans adeptly adjust its texture in alignment with the surrounding weather. After the final application, all items are once again kept in a furo ensuring perfect drying and an impeccable finish.
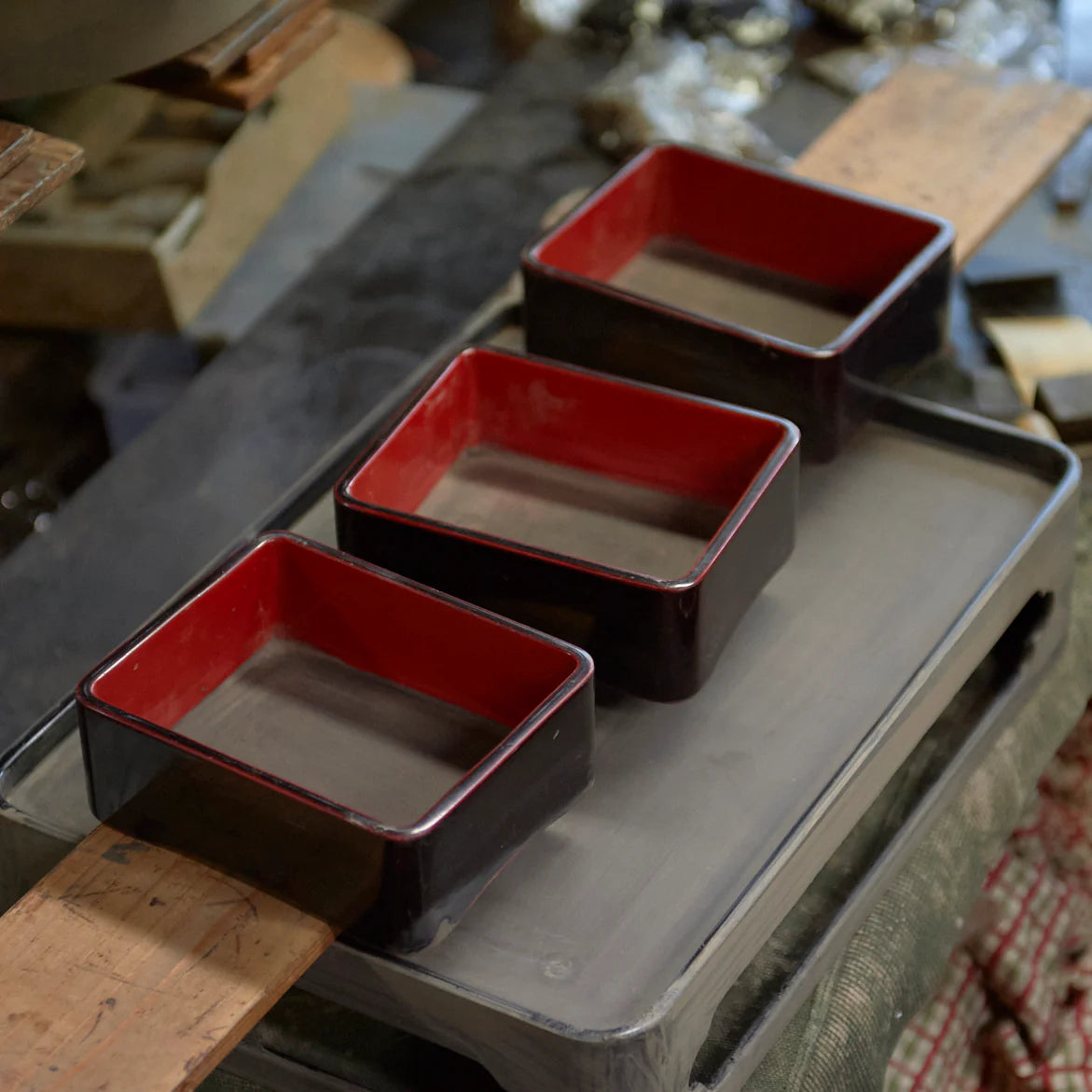
Decorative Adornments
Exquisitely, some Wajima lacquerware pieces are completed with detailed adornments.
The chinkin technique involves carving fine designs onto a lacquerware surface, then filling these etchings with gold or silver powder, adding depth and highlights. Maki-e, another method, entails artisans painting with colored lacquer and then embellishing with metallic powders. Thetaka-maki-evariant introduces granular details for additional depth. These refined techniques, paired with the depth of the lacquer, bestow Wajima lacquerware with its celebrated and lasting beauty.
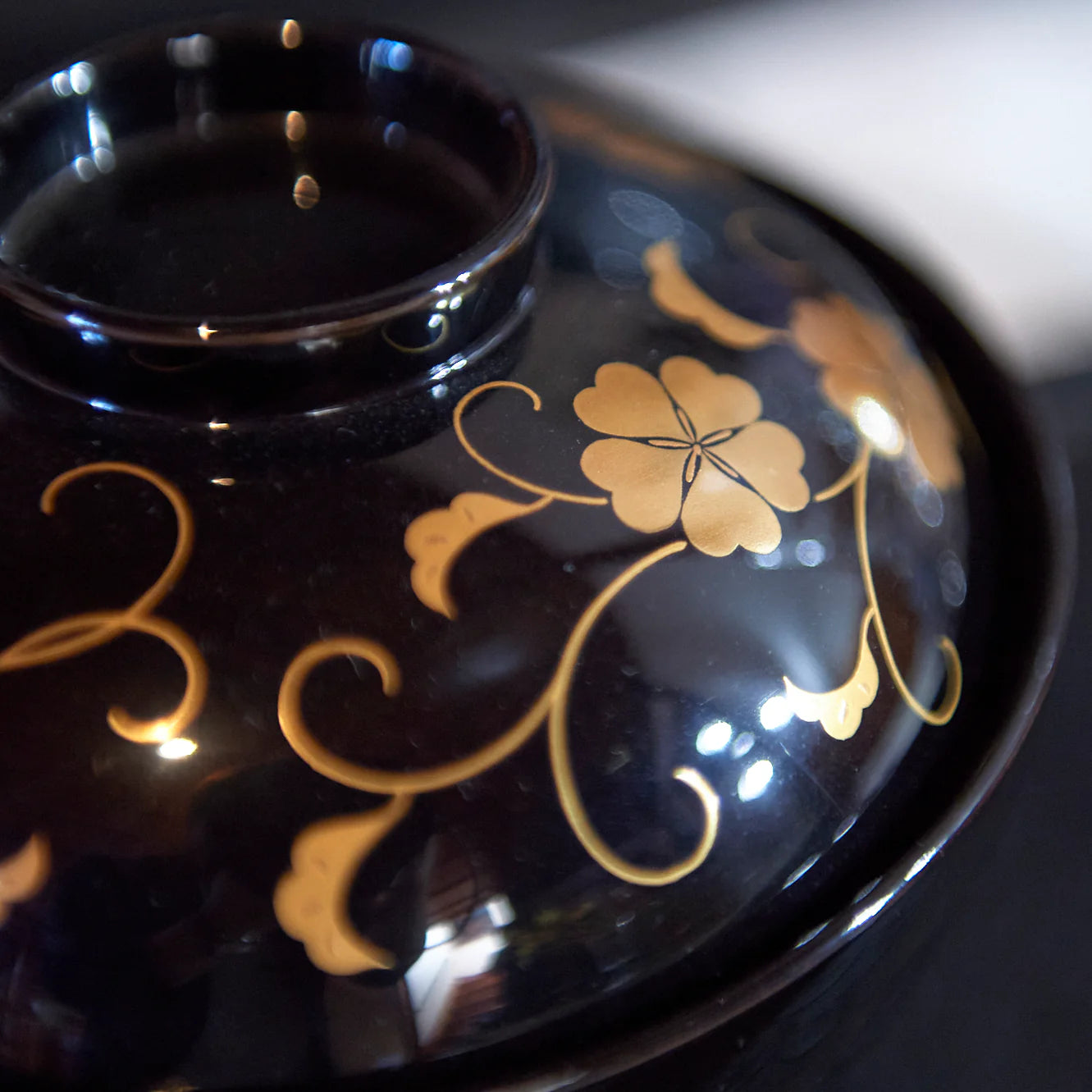
Makers
Related posts
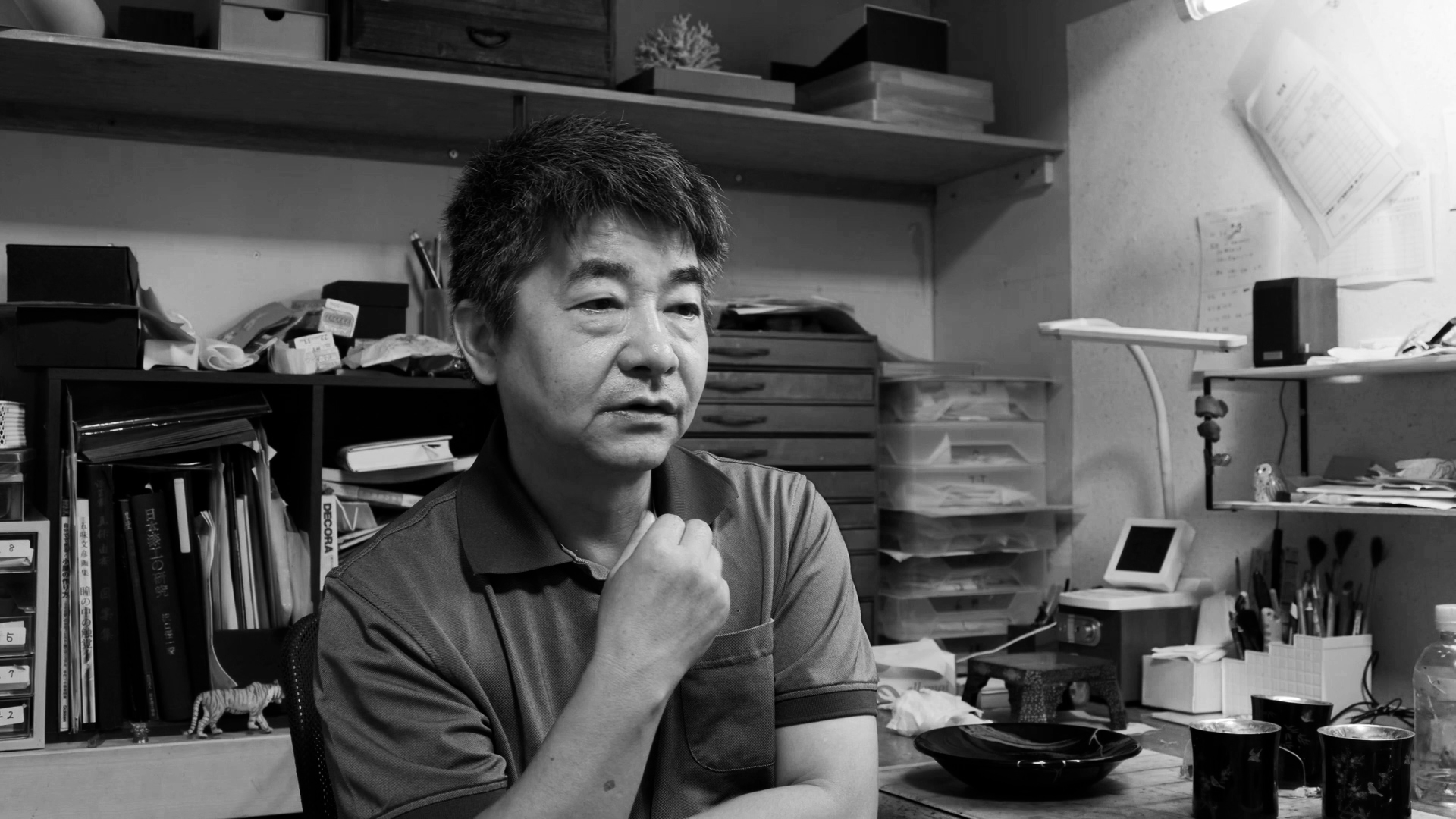
Meeting the Master of Raised Maki-e: Where Gold and Artistry Shine as Wajima Lacquerware
Discover Yamanoshita Akihiro’s raised maki-e lacquer art, crafted with precision, skill, and deep Wajima tradition.
Read moreFilters