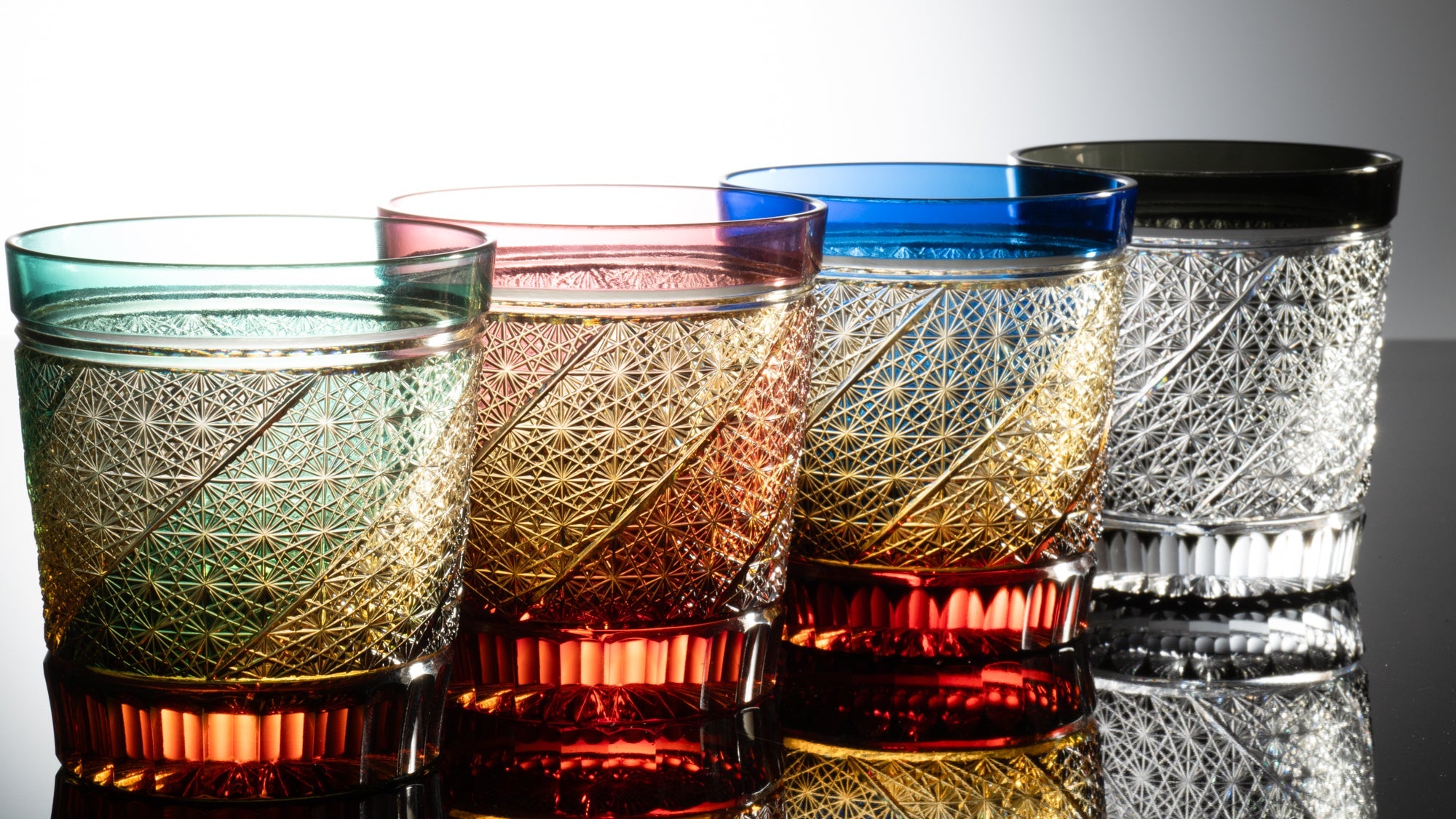
Precious Crystals of Edo City
Edo Kiriko & Edo Glass
Tokyo, the capital of Japan, is also a hub of craftsmanship. Among its many traditions, Edo Glass and Edo Kiriko are types of glassware that have been passed down for around 200 years in Edo—the former name for central Tokyo.
Their luminous surfaces echo centuries of craftsmanship, born in what was once Edo and still thriving in modern Tokyo.
About Edo Glass
Edo Glass is a handmade craft that carries on techniques passed down since the Edo period. Unlike mass-produced items, each piece is one-of-a-kind, shaped with subtle variations and warmth that only handcrafted work can offer. These pieces are made by skilled artisans in areas around Tokyo, and their quiet beauty has earned them popularity both in Japan and abroad. In 2014, Edo Glass was officially recognized as a Traditional Craft by Japan’s Ministry of Economy, Trade and Industry.
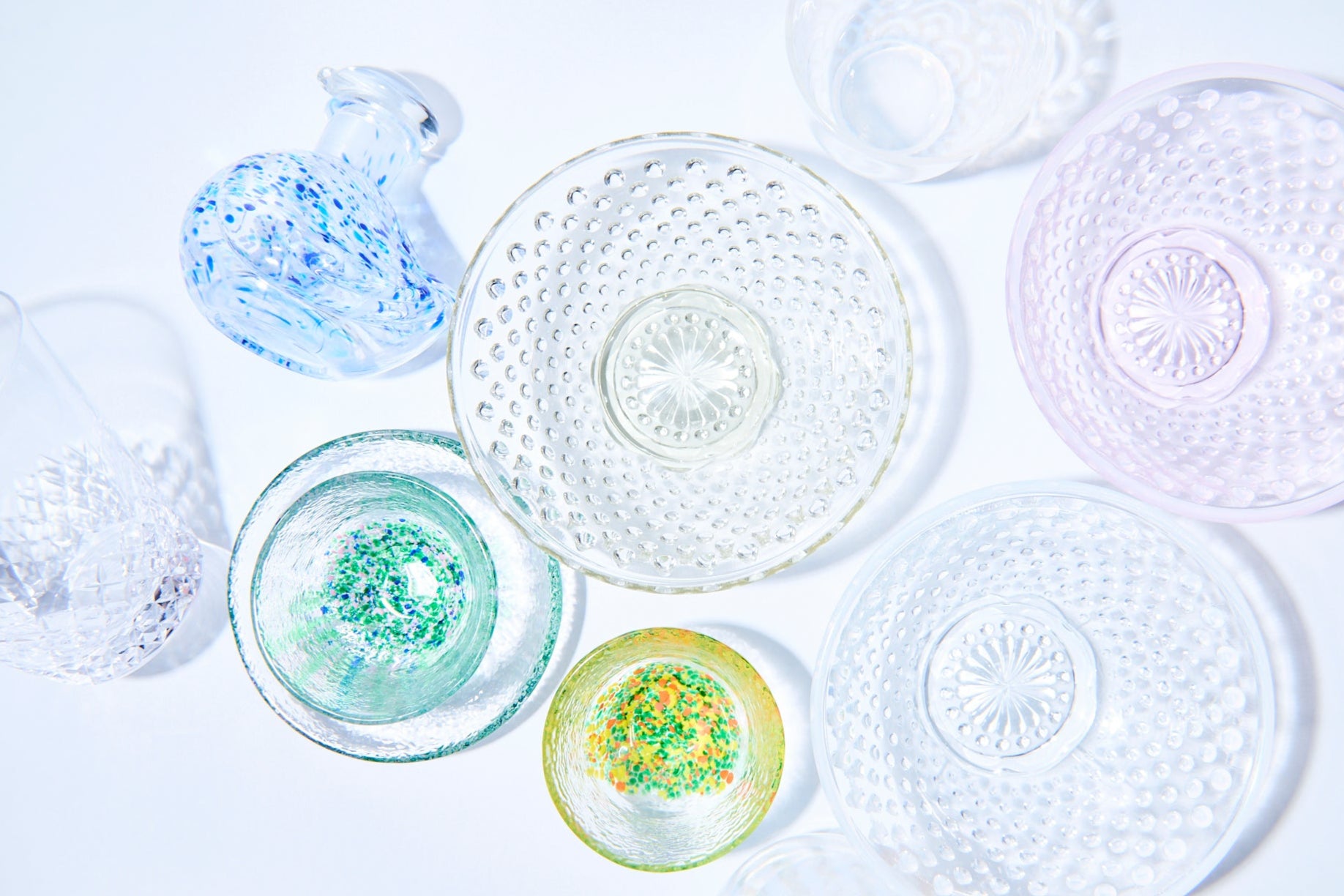
History of Edo Glass
Glass first arrived in Japan through Portuguese and Dutch imports during the Sengoku period (1467–1600 CE). Blown glass production began in Edo (today’s Tokyo) around 1711, and by the 18th century, glassware like wind chimes, kanzashi, and sake cups had become part of everyday life. In 1879, Tokyo saw the rise of Western-style glass factories, but many workshops were later lost to major disasters in the 20th century. Even so, the craft endured—and today’s Edo Glass carries on that legacy, piece by handcrafted piece.
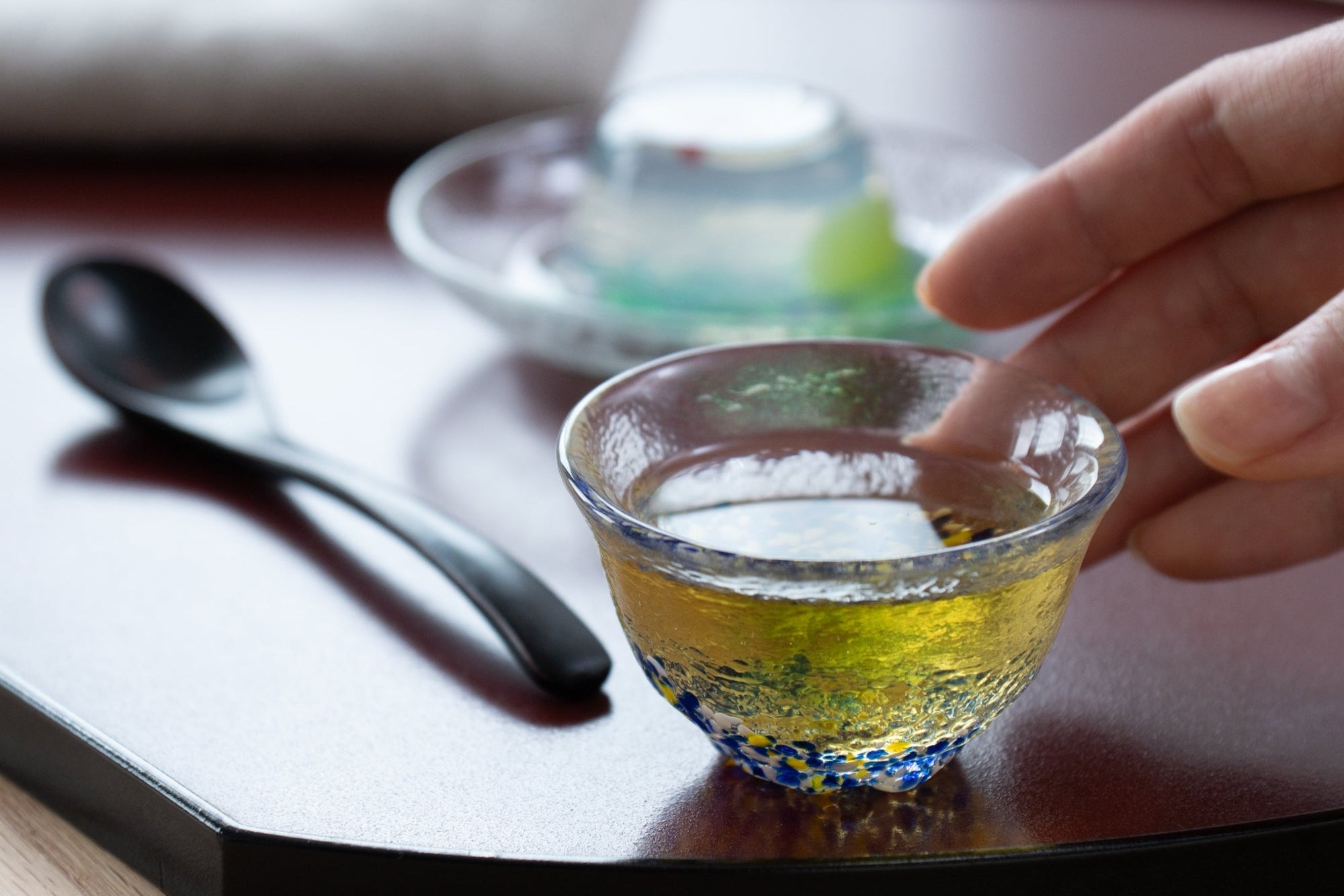
About Edo Kiriko
Edo Kiriko is a traditional craft where intricate engravings are made on the surface of Edo Glass. Around twenty geometric patterns are carved with remarkable precision, creating a jewel-like brilliance as they catch the light. Especially in pieces made with colored glass, the contrast between the vibrant surface and clear glass creates a sharp, striking effect. These refined cuts are made without detailed sketches—only simple guidelines are drawn directly onto the glass, a method unique to Edo Kiriko. Edo Kiriko was officially designated a Traditional Craft by Japan’s Ministry of Economy, Trade and Industry in 2002.
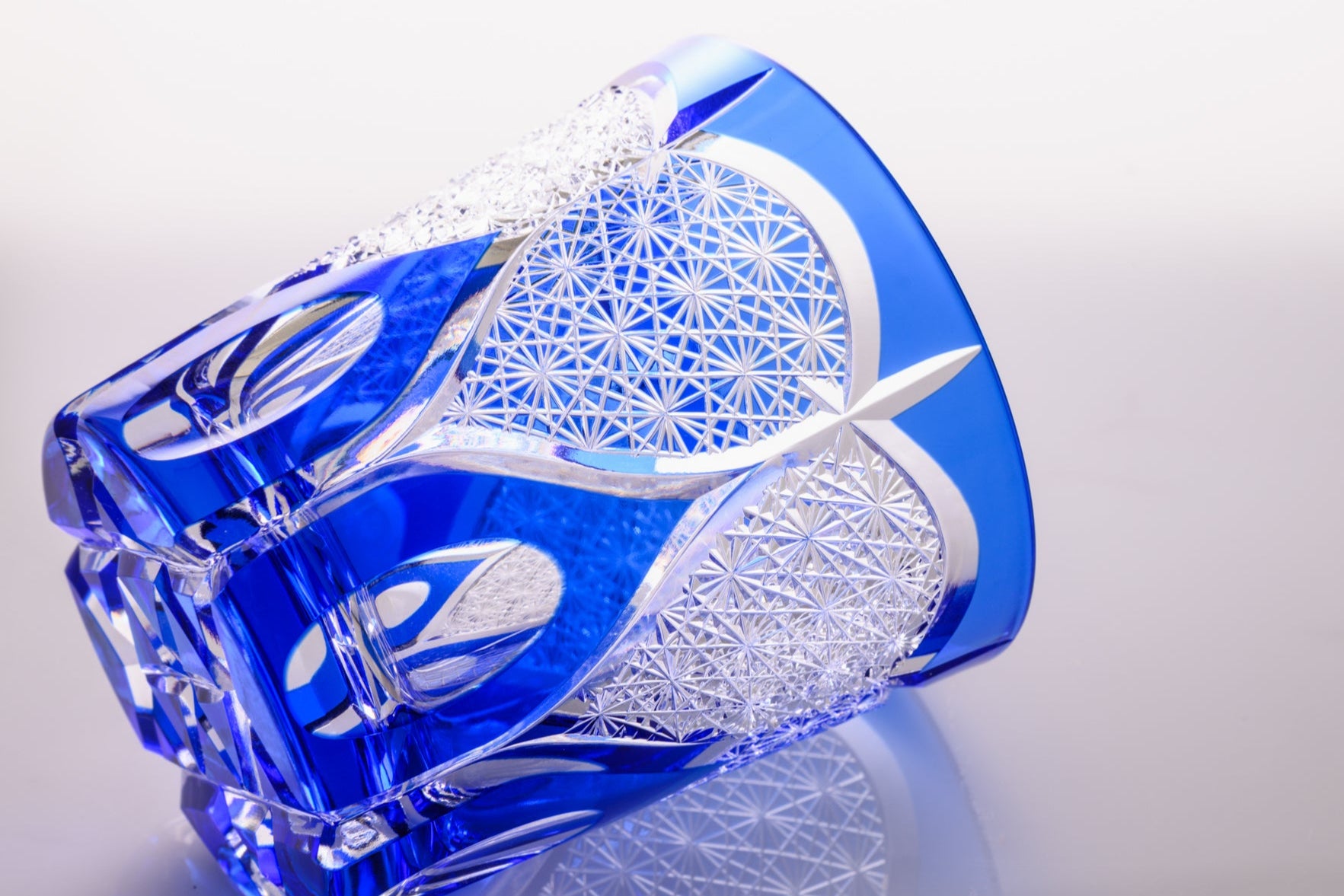
History of Edo Kiriko
Edo Kiriko began in 1834, when a glass merchant named Kagaya Kyubey first etched glass with garnet stone powder. The technique matured in the Meiji era, when English glass artisan Emanuel Hauptmann introduced Western methods. Eventually, a signature style emerged: deep cuts on colored glass layered over clear glass. From the Taisho period onward, Edo Kiriko grew into a beloved decorative art—one that still flourishes in Tokyo today.
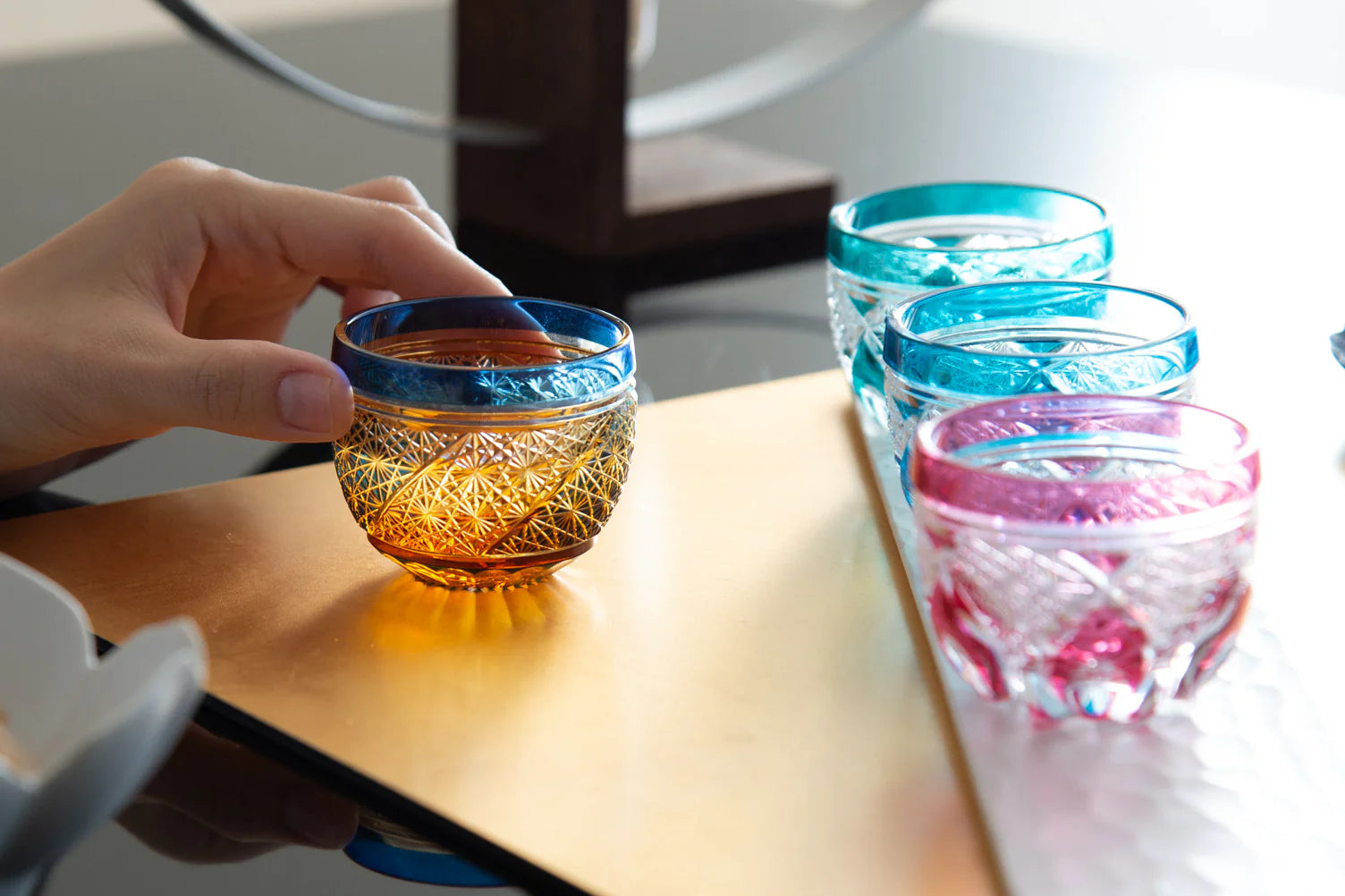
Crafting of Edo Kiriko
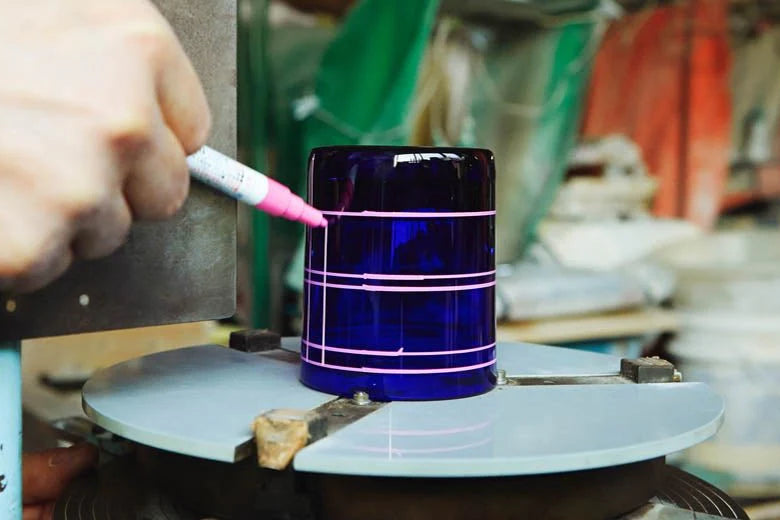
Waridashi/Sumi-tsuke
In the production of Edo Kiriko, no detailed sketches are drawn for the design. Instead, a process called waridashi (dividing) or sumi-tsuke (inking) is used to mark the layout directly on the glass. These marks are then followed by lightly carving thin, shallow lines with a whetstone wheel to serve as the foundation for the final pattern. From these faint lines alone, the intricate motifs of Edo Kiriko are brought to life.
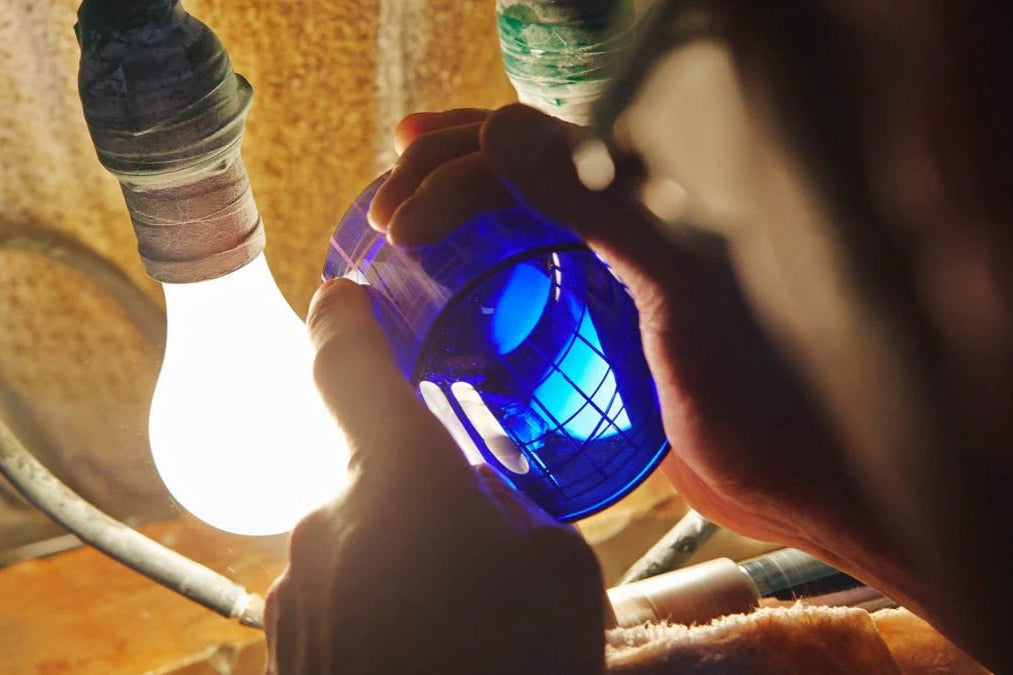
Arazuri – Sanbangake
For Edo Kiriko engraving, artisans use kongo-sha, a coarse garnet powder, along with rotating metal wheels. In the initial stage called arazuri, the design is carved roughly using the coarsest grain. This is followed by sanbangake, which uses finer abrasives to refine the lines. Although no rough sketch is drawn, the thickness and depth of each cut are achieved with remarkable precision, guided solely by the craftsman’s skill and sense of balance.
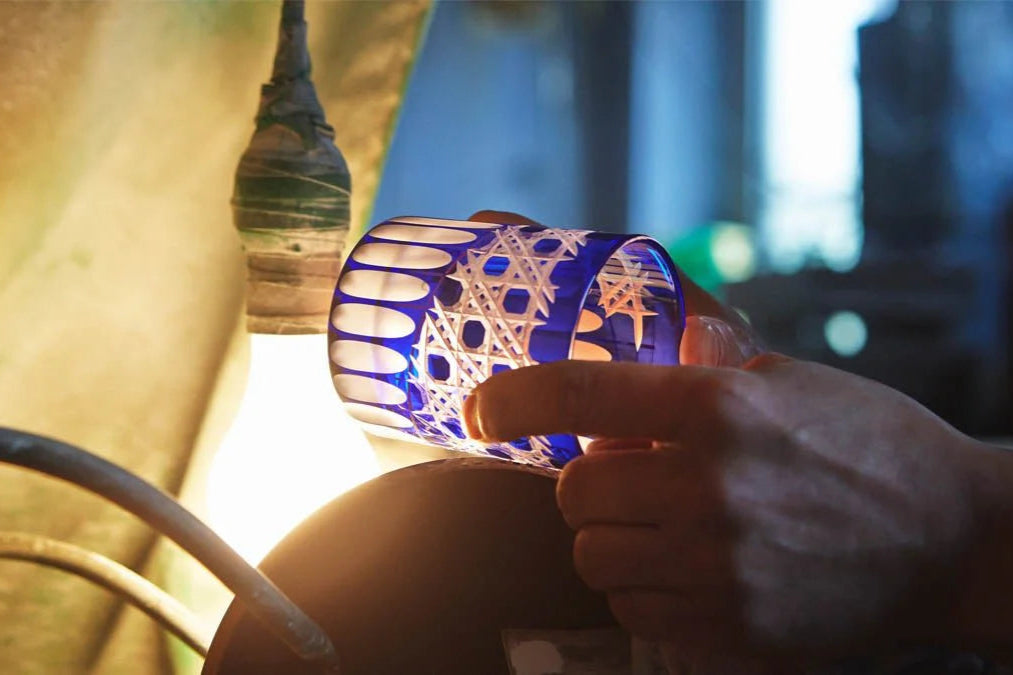
Ishikake
In the final carving stage called ishikake, patterns from earlier steps are refined using a whetstone disk. This process smooths the engraved surface and allows for intricate details that can’t be achieved with metal wheels. As the final cutting step, ishikake plays a key role in determining the clarity and finish of the piece. The work must be done with great care to avoid leaving behind any coarse marks.
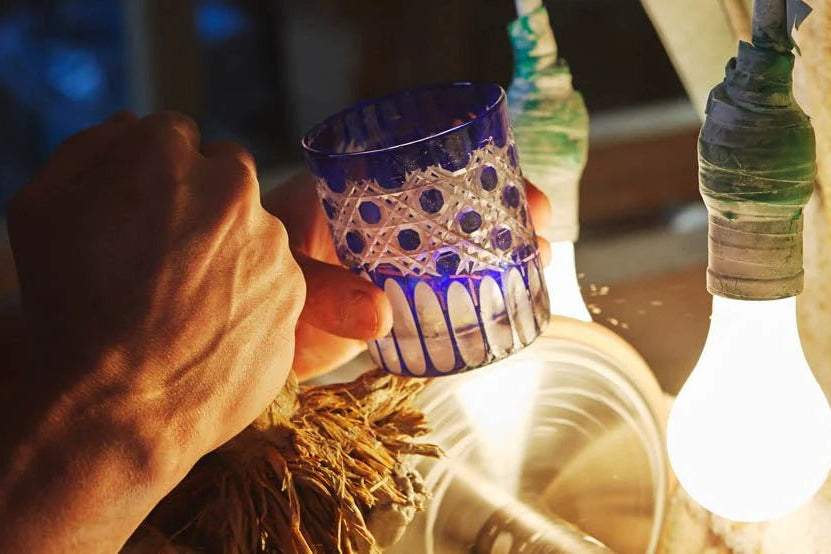
Migaki
After ishikake, the surface of the glass appears cloudy, like frosted glass. The polishing stage, called migaki, restores transparency and brings out Edo Kiriko’s signature shine. Using water and polishing powder, artisans polish the piece with wooden disks made of paulownia or willow, as well as bristle or belt disks tailored to the design. Finally, a cloth buffing wheel—known as a habuban—is used to create a glossy, refined finish.
Makers
Related posts

Glass from the Past: A Visit to the Hirota Glass Japanese Glass Museum
Journey through time at Hirota Glass Museum, where the legacy of vintage Japanese glass comes to life.
Read more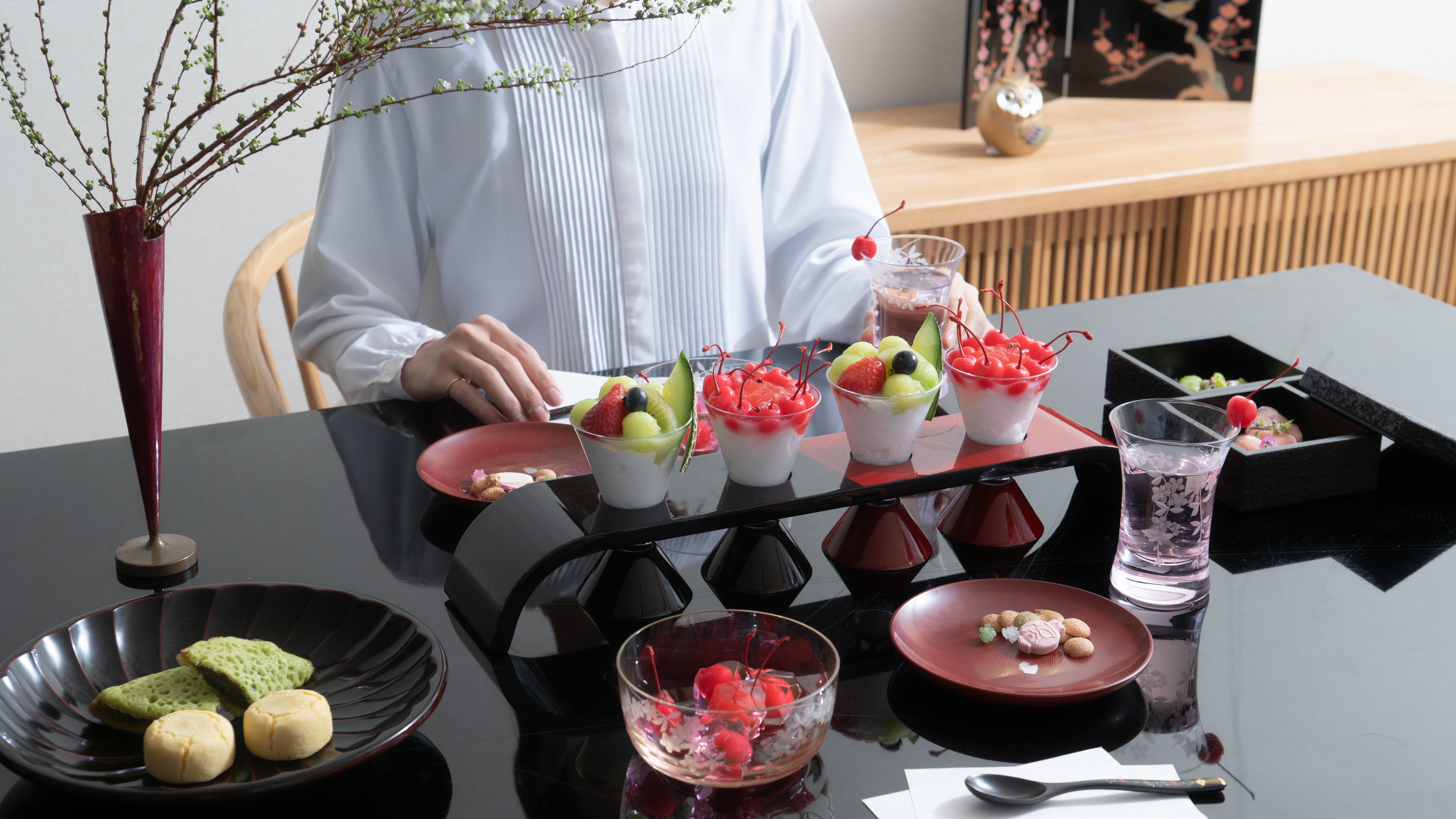
Refreshing Tea Time: Cherry Desserts with Edo Kiriko Cut Glass
Create a refined tea time with Edo Kiriko glass tumblers and glossy lacquerware tableware.
Read more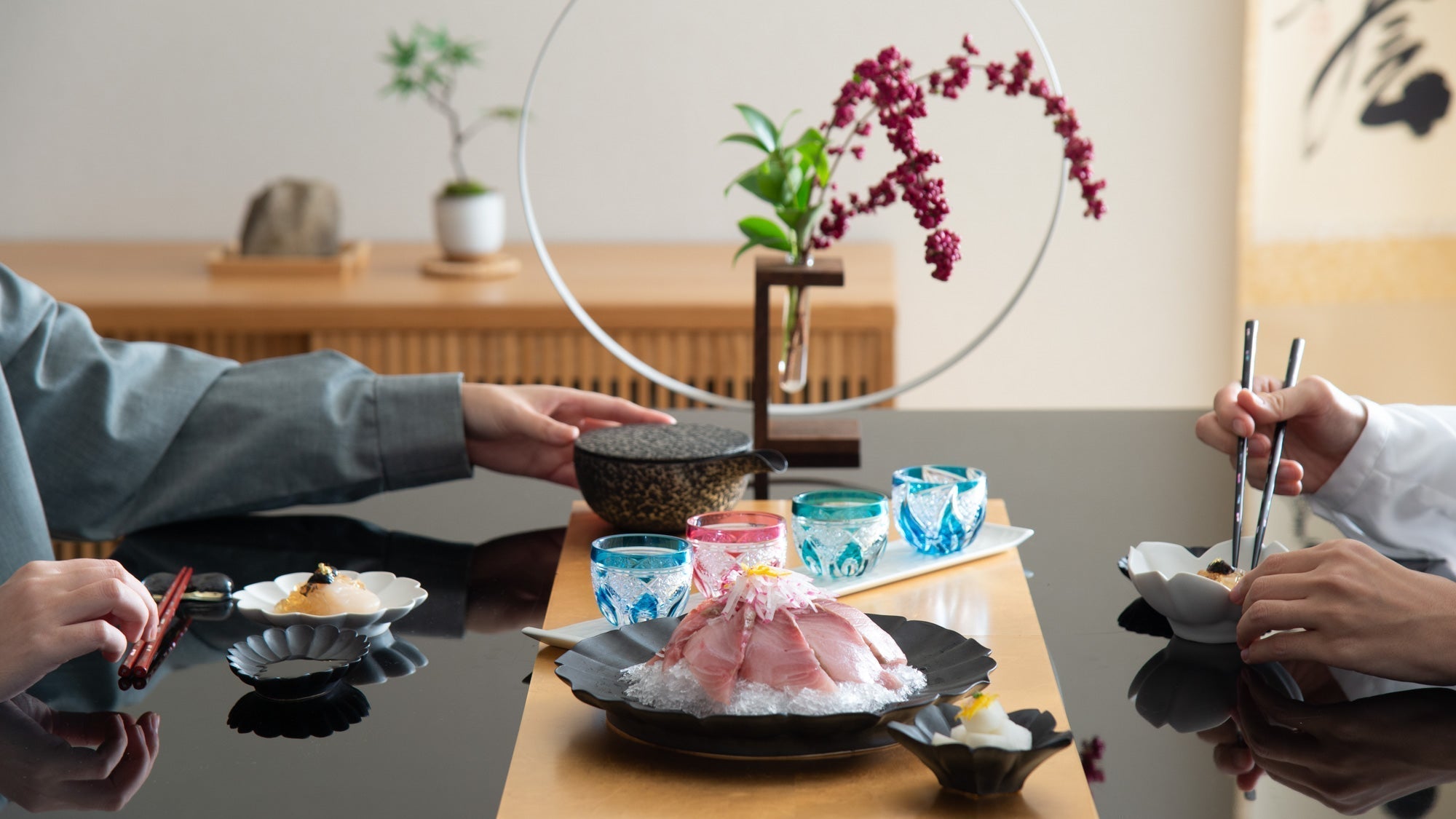
Exquisite Sake Experience with Edo Kiriko Cups
This table setting is sophisticated and vibrant with the addition of colorful, luminous Edo Kiriko sake cups.
Read more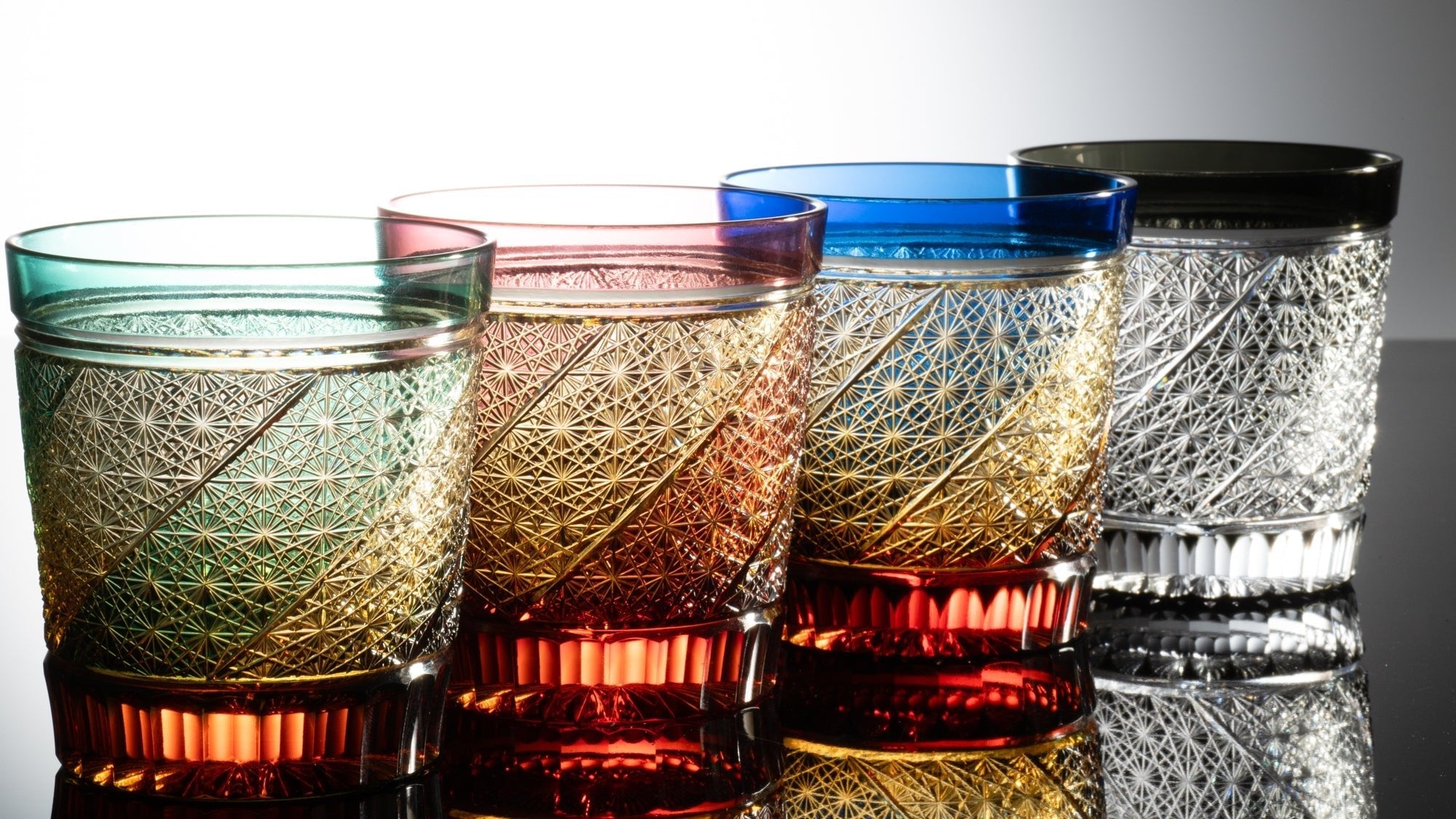
Possessing the Light, Edo Kiriko Glassware
Explore Edo Kiriko with artisan Kiyohide, where traditional glass cutting meets precision, beauty, and craftsmanship.
Read more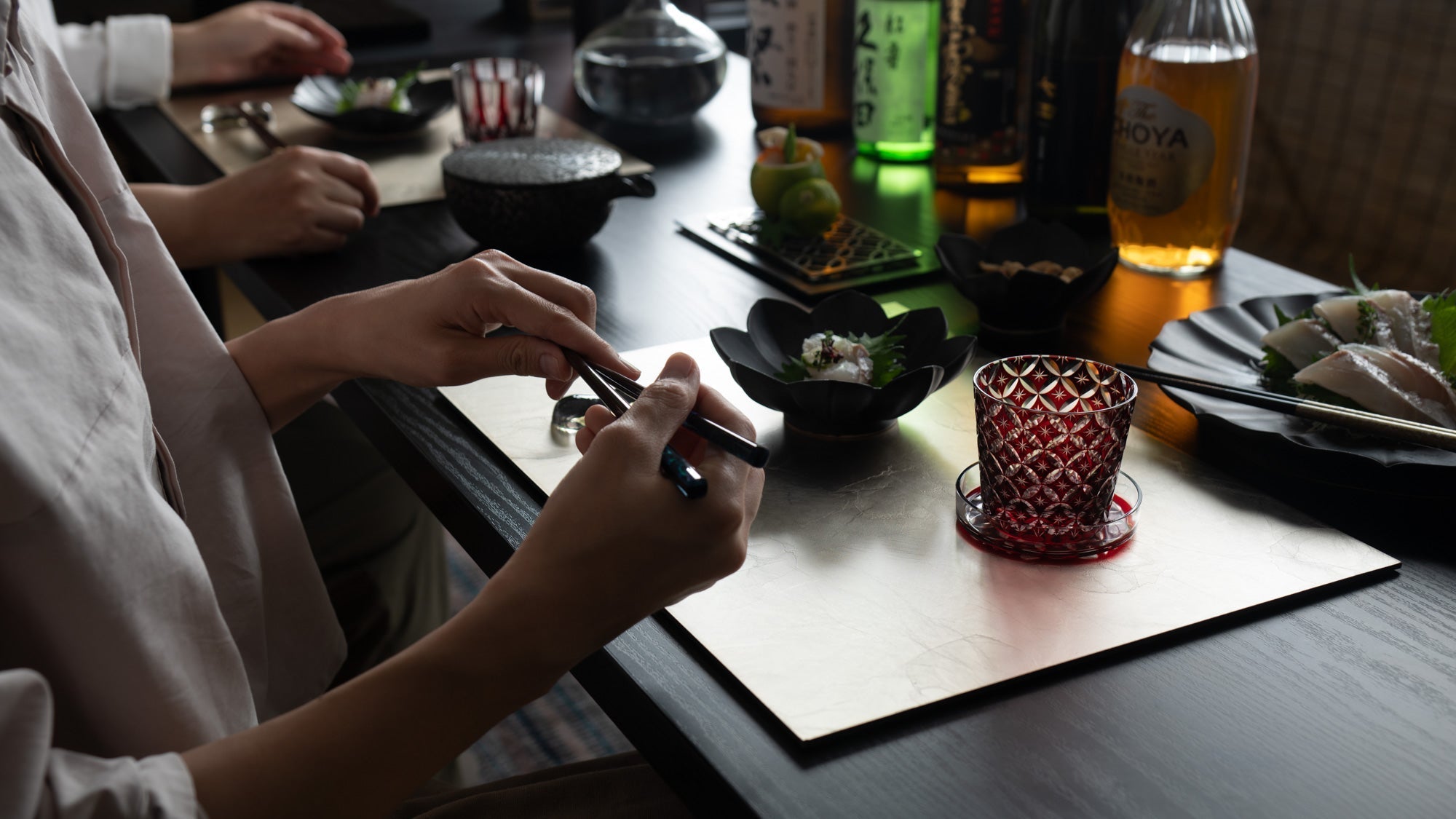
Captivating Contrasts: Glimmering Edo Kiriko Glassware on Black
Create a luxuriant ambiance with the beauty of opulent drinkware accompanied with Japanese food on stylish tableware.
Read more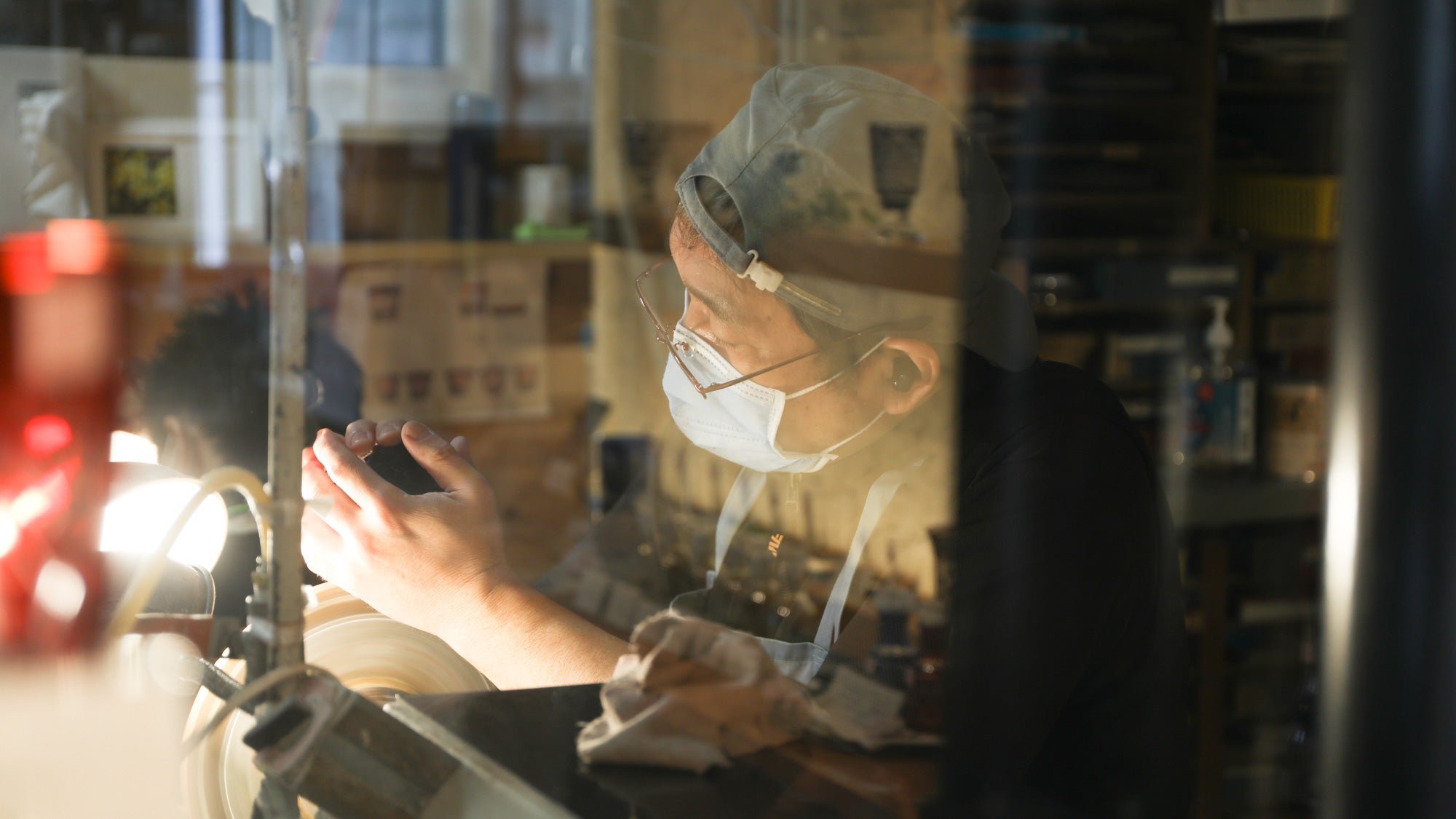
Discovering Edo Kiriko with Mr. Tatsuro Hirota, President of Hirota Glass Co., Ltd (Part 1)
Step inside Hirota Glass and explore the craftsmanship, history, and future of Edo Kiriko in Tokyo’s Sumida Ward.
Read moreFilters